.png.2d845ce5c3e86de370a7d3eb81cffae2.png)
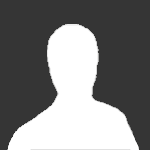
Alchemyjim
Members-
Posts
106 -
Joined
-
Last visited
Content Type
Profiles
Forums
Gallery
Everything posted by Alchemyjim
-
I need some help with Barndominium steel structure?
Alchemyjim replied to lms_jam's topic in Seeking Services
Here is one I did recently in Northern California. (No Snow Load) The steel building manufacturer said you can have X amount of windows, doors and skylights. As long as they do not interfere with any of our support beams you can place them where ever you want. I took the plan they provided and created a chief model with the steel framing in place. Then I added a 2x6 interior wall just inside the steel structure for the living area (do this by adding a 2x6 interior wall with a 2" air gap to the exterior wall). I do not recommend trying to wedge in 2x framing between the horizontal steel girts at 16" o.c. Not only is it a pain and labor intensive but having a traditionally framed wall allows for the elect, plumb, mech. to go smother, it also creates a barrier between the steel siding and the insulation. That is always a traditioned condensing point. You lose some square feet but that is a huge building. Basically find a steel building contractor that is a factory rep. They will give you plans to start from. Then go from there. Good luck. -
The biggest downside to the shipping container house is the fact that your are making a conditioned space inside a steel box. It WILL sweat unless you add at least 4" of closed cell spray foam.
-
You could get it done with the material editor tool. Change the roofing and siding to no pattern...
-
U.L. listing for one hour wall (Stucco and 5/8" type 'x' gyp)
Alchemyjim replied to dshall's topic in General Q & A
They are asking for that much more lately. I submitted this to the city of Hayward. It seemed to work... -
Closed cell is R-7 per inch. The min. roof insulation in our climate zone is R-30. So you only need about 4 1/2" thick from the underside of the roof ply.
-
In California it is 1sqft of vent per 150sqft of conditioned area. Same for roof as for crawlspace. It is important to note that the 150 sqft refers to floor plan area, not the surface of the roof planes. Venting should be about equal at top and bottom. If you have 1-1/2" gap at the blocking, multiply that by the length of the roof. (18sqin per foot) That is the lower number. The cora-vent V-600 has 20sqin of vent area per liner foot of ridge. Multiply that by ridge length. Those numbers should be kind of close for it to work correctly. Keep in mind the ridge is venting two roof planes. The building department hardly ever looks at the ratio between upper and lower, but the combined vent area must be greater than 144sqin per 150 sqft of conditioned area. A better option is to use closed cell spray foam insulation. It depends on the jurisdiction and climate but I have successfully specified it in Humboldt and Monterey counties. Sometimes they require that you can prove it's efficacy. So I send them the technical data (like attached) and they approve. It sounds crazy not to vent a roof. But look into the "first condensing barrier" and see how closed cell eliminates that. Fascinating building nerd fodder. Essentially it causes the heat to slowly cool as it moves through the foam instead of hitting a hard cold surface immediately. Thus not creating condensation. Also batt insulation loses A LOT of it's R-value when air passes over the unfaced side. Venting the cavity creates an air current that pulls the entrained air from the fiberglass batt. That entrained air is how batt insulation works. Closed cell will cost more but it eliminates the need for vented blocking, baffles and ridge vent. The framers and engineer will like that. I have been building and designing roofs like that for years and never had a call back. But they have all been in California. I am really not sure if the same methods would apply in Louisiana (humid) or Minnesota (frigid). Heatlok HFO High Lift TDS_19.pdf
-
In some jurisdictions it is 12 months between inspections. Which means you can get the framing or rough plumbing inspected, then you have a year to drywall. I've known a few projects that carried over into a few years this way. This may work for you but there will be no occupancy certificate. As far as the drywall goes, only the walls that are specifically called out as a fire rated assembly (between garage and living area for example) need to follow the specific UL listed construction. For everything else 1/2" is fine. However without drywall you will not have finish electrical or plumbing. Not sure about the IBC but the California code -"R702.3.5.1 Screw Fastening" means you need an inspection of the drywall screws or nails. So no way to get a final without that. And finally kitchens and bathrooms need a smooth, non-absorbent finish. So no final without paint at least in those rooms.
-
Highly Ornate Wrought Iron Driveway Gate Part II
Alchemyjim replied to John_B's topic in Symbols and Content
Well done. -
Hi Designer1. I can share my experience with plan sets if it is not too boring. Excuse me if it gets long winded. Just thought I'd give you my perspective. I started (like most of us) on the "dumb end of a hammer". Then after years of seeing the old timers take 10 aspirins a day so they could keep working I decided that although I loved the work I didn't necessarily want to be climbing scaffold in the rain when I was 60. (Lots of fun in your 20's though)! So I got Chief Architect and 6 years later that's all I do. You need to look at a completed construction project like a good novel. The plans are the cliff notes. It starts with a page of contents, moves to an introduction, then the details come in. All while not getting bogged down by making it an IKEA manual. The denouement of the novel is when the client walks through the finish product for the first time. There is not a lot of information on this topic but I believe that the plan set is an artistic interpretation of a very complex object. For example lets say a house has over a million pieces. Every nail, piece of plywood, insulation batt, gas pipe fitting, etc. Can you image a plan set showing clearly all of these elements? That would be ridiculous of course. However you also need to consider everyone from the client, planning tech, contractor, plumber, surveyor, etc. using this set to complete the puzzle. Add to all this the fact that you need to cover you butt. You don't want to specify some waste line arrangement in a remodel where you can't actually verify what the existing pipe looks like. So how do you satisfy everyone? I really don't know. My plan sets are constantly evolving. You think you have it figured out and then a plan checker shows you some new code they are adopting or a framer asks if you can show the hold-down locations on the foundation plans, so you just adapt. Chief Architect has infinite layers and plan view sets and there is very little it won't do if you ask it nicely. The real conundrum is making sure you have a good idea of the time commitment the project will take from you and you are able to communicate that to the client before you begin. I would love to hear any other chief users feedback on this.
-
Here on the central coast of California (Monterey) the building department usually requires detailed gas schematics on the plans. From the meter to every appliance you need to show pipe sizes. I show the lines on the plumbing plan then provide a separate schematic with size call outs. The math to get the pipe diameter can seem tricky put there is a chart in the plumbing code that makes it fairly easy. This one was medium difficulty. Just finished a 10,000 sqft house with 10 gas fireplaces and a pizza oven. That was a bit harder. The trick is to create the gas line on the plumbing layer, then copy that into a detail window to add text. Good luck.
-
Hi Lindsay, You have to build the foundation first. Once that is done you can open the garage room dialog box and you will be able to change the stem wall height in relation to the slab. See attached...
-
numbering different plan check response revisions
Alchemyjim replied to JoeinNorCal's topic in General Q & A
Here is how I do it. Create a designated space in your title bar. Revisions from the client or engineer usually end up changing the revision number (1.6,1.7, etc.). I call any corrections from the building department an RFI (Request for information), most AHJ's do that anyway. Then add a revision cloud and triangular call-out where it occurs. One thing to note, in the area I work after three revisions they make you re-submit. Probably a good policy so the plans don't end up a jumbled mess of revision clouds. And honestly if you get four major RFI's it might be time to rethink your process. I'd love to see how my other chief family accomplish this. Always open to better ways. This forum is great for that. All of us growing together. -
Twinmotion has its value. Especially since I signed up last year when it was free. If you play with the setting enough you can get some decent images out of it. Like this one...
-
Hi everyone. I need a chiefer to make an as-built from a matterport. Attached is the basic floorplan. One story, pretty easy. I will send the matterport link to the designer. I will need accurate wall finishes, flooring, doors and windows, trim, cabinets, fixtures, etc. The works. Let me know rates and about how long you think it would take. I get these all the time and it could turn into semi-regular work for the right person.
-
Hi Joe. In Monterey here. They always ask for that. Not sure why this is viewed as some "big government" intrusion. You want to know the miles per gallon for a car. Why not pay attention to home energy use?
-
I am giving robdyck an upvote even though he has two first names.
-
I make custom layers for things all the time. Usually they are project specific. It helps to start every layer name with a space. That way all the custom layers associated with the project are at the top of the list.
-
I have been using chief for a few years. Just recently wrapped my head around Saved Plan Views. I feel like an idiot for not using them earlier. Chief is really like an onion. Every time you peel off a layer you cry a little bit for not realizing something sooner.
-
I would see if there is a local person that can create a Matterport scan of the place. Then any remote CA user can build an accurate As Built.
-
2020-04-11 16-10-33.mp4
-
Hi everyone. I found an interesting way to show topo lines in 3d. It is especially helpful when showing how a building will be cut into a hill. I transform the elevation lines and turn them into rope lights. Copy Elevation Line, Convert to Polyline, Convert Polyline, Select Rope Light. You can even adjust light value and play with it in Standard or PBR. Good times. 2020-04-11 15-58-28.mp4
-
Hi All. I have a question that is not necessarily Chief related. More of a code question. A client with a physical disability would like to remodel their garage into a large accessible bedroom. Because of his disability he needs a toilet and vanity in the room. Is anyone familiar with the code on this? Would you need to apply the bathroom codes to the bedroom? So many questions. It is in California. Thanks
-
The new version is slick!
-
This is one of those instances where it must be drawn with polyline solids. Make sure you create a layer called "Steel Framing" or something similar to place all these pieces. Once you have mastered the polyline solids this is relatively simple.