.png.2d845ce5c3e86de370a7d3eb81cffae2.png)
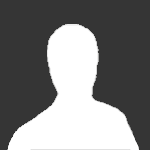
Alchemyjim
Members-
Posts
103 -
Joined
-
Last visited
Reputation
38 ExcellentAbout Alchemyjim
- Birthday December 23
Contact Methods
- Website URL
Profile Information
-
Gender
Male
-
Location
Monterey, CA
Recent Profile Visitors
4667 profile views
-
TeaTime you rock!
-
Hi all, quick question... My toolbar got goofy and I lost an icon which I cannot find. Between the page up and down arrows there should be a square displaying the layout page number. I CANNOT find it in the toolbar menu. I know it is probably right in front of my eyes. Thanks for your help.
-
Things evolve. Do we still nail down a board at the entrance to hold the thresh? Yet we still call it a threshold. Do you know what they used to call Brazil nuts? Both antiquated terms but the horridly offensive one fell out of usage for a reason. I just use Bedrooms 1, 2, 3 etc.
-
This is a 30' yurt kit on a wood framed deck platform. Done 100% in Chief Architect X15. Just thought I'd share in case anyone was looking for yurt ideas. It was easier than it looks. The walls are 1/4" fabric over a custom lattice material as the framing layer.
-
Or.. Make an octagon, 5' side length, place it, snap your walls to it.
-
Resilient channel or other acoustic wall detail components
Alchemyjim replied to MovingandShaking's topic in General Q & A
Every case is a little different. I add the appropriate layer to the walls and/or ceiling. For instance in the wall DBX I'll add a 1/2" space behind the drywall for RC. Perhaps it will need to be a double wall. Then take a cross section and detail it. If the wall is built up correctly then the detailing should be easy. -
SpellCheck made us terrible spellers, AI will make us just terrible.
-
These were done in X14. No post production. There is some light bleed. If I spent some more time I could probably eliminate that. I agree that exterior rendering in Chief is not quite there yet.
-
Would a cricket with two planes work? Low slope with a valley in the middle.
-
Hello all, We are in search of a competent Chiefer that can create accurate As-Built models of homes located on the Central Coast of California. The model would need to be created from exterior pictures, google earth and a Matterport. X-14 preferred. Accuracy is very important. The Matterport should be sufficient for the interior portions but the model will also need reflect correct roof pitch, framing, fixtures, cabinets, etc. I look foreword to any queries. info@montereybuildingdesign.com
-
Another tip. If you are using P-line solids for the shelves, make sure their elevation is set to absolute. If you make them outside the niche they will be set in relation to the floor. Once you drag them into the niche they will move up or down.
-
Thank you everyone, This has been very informative. I think many of us in the industry (including building officials) have been using different methods. It sure complicates matters because this means a 10' x 10' shed is actually 100.7 sqft. But ANSI Z675 clears it up. It is indeed 100.7 sqft. Wild but true. Perhaps this is a good suggestion for Chief as it measures sqft area from exterior framing which is not the code. Maybe an option to create a polyline that includes siding?
-
Hello everyone, I have been in construction for 20 years and I had the first building department say that the floor area is measured to the exterior of the siding. For every project I've ever been on I have measured to the exterior face of the framing (essentially to the edge of foundation). This is a new one to me but sure enough it is in their code (Santa Clara County, CA). Has anyone else run into this? It is kind of a big deal. For example a 30' x 30' house should be 900sqft. But if you add sheathing, house wrap, siding etc., it is 912 sqft. I am working on a 5,000 sqft residence with a convoluted shape and thick stucco cladding. This would add another 77 sqft. Thanks and appreciate the feedback.
-
I have found the easiest way is to create another "ELECTRICAL NOTES" folder, then just cut and paste everything inside the older one into it. Not very elegant but is pretty quick. Then make sure these folders are in you template file so you will have them for every new project.