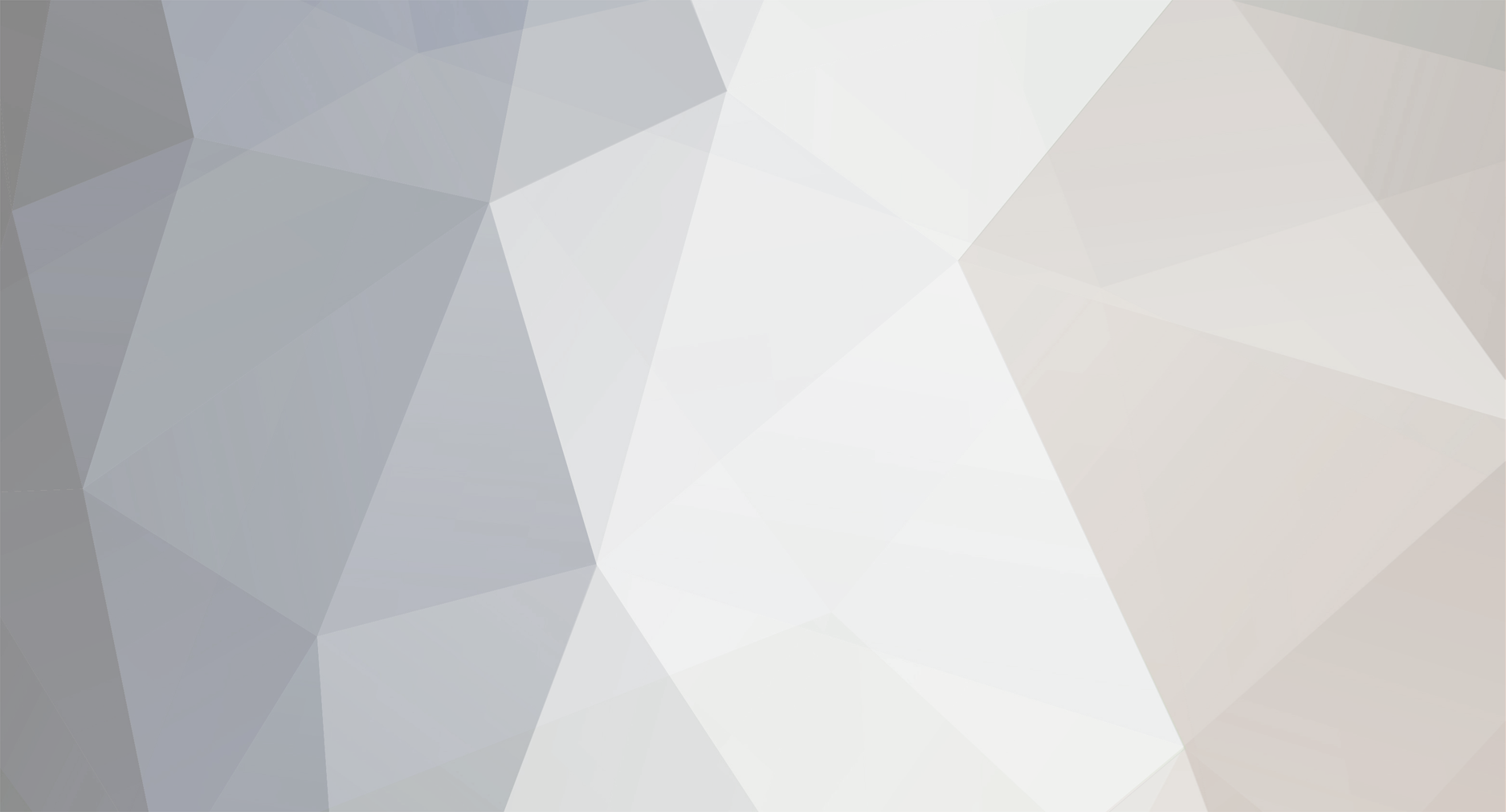
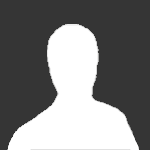
ValleyGuy
Members-
Posts
325 -
Joined
-
Last visited
Content Type
Profiles
Forums
Gallery
Everything posted by ValleyGuy
-
The separate window layer only takes care of the windows not showing. Only doing this step will leave the opening lines. Turning the wall lines to white should make all of the wall opening lines the same colour as the background page.... unless your background isn't white. What colour are your 'doorway opening' lines?
-
This might work for you, all on the same floor.
-
Best Practices for Storing and Applying Keynotes and Notes
ValleyGuy replied to skoz44's topic in General Q & A
For General Notes: I have a text box in my plan template on a CAD sheet - all the stuff that shoves some of the legal responsibilities back onto the General Contractor, things like verification / changes / dewatering monitoring and documenting / engineering... general code compliant designer responsibilities that are usually beyond our control. This is embedded into the Layout Template and is always present. It rarely changes and basically spells out that the general contractor is responsible to know, understand, and follow all of the local governing compliances. For Key Notes: I just use Note schedules like Alan has above. However, I drive all the note information from the Saved Plan View. I don't arrow up and down between floor plans, each floor plan has it's own Saved Plan View. This creates independent Active View Defaults, to which I can use the Edit Active View button and have made Note Defaults for each SPV. I make a Note Schedule for each floor and leave all the schedules on one common saved CAD sheet. I leave each schedule populated with the common items and when I drop a note on a particular floor - because I'm on that specific saved plan view, it automatically picks up the appropriate note number and populates the appropriate schedule. I may have 10 notes on the main floor and only 6 on the upper floor. The common things like 'Grab bar blocking required' (as was requested by the building officials to be on the plans) doesn't need to be typed in as it is already saved in the schedule. Items like ' In-floor electrical heating mat under ceramic tile' only takes a minute to type - usually less time than searching for a cut and paste. Saved CAD sheets also have their own Active Defaults that I have also made specific note defaults and specific note schedules for, just like SPV's. Drop a note on the CAD sheet and it will populate that schedule to then be sent to the layout. Driving the Note Defaults from the Saved Plan View works well for me with revisions too. I have a SPV for Revisions that also has it's own Note Defaults and Note Schedule. When I'm with a customer and they want to change something, I switch to the Revisions SPV and drop a note, the note has it's own shape and is coloured red, it automatically populates the red coloured Schedule I have saved in the plan under the drawing for easy review. One thing I try to do is not over think the key notes and draw a line at what information needs to be relayed. I tend to include code items requested by the building officials, customer selections, and items To Be Determined. For example, I don't put stair code in a note schedule as the specific plan rise and run are noted in the stair detailed drawing. Code stair min and max sizes are just as important as the size and length of the nails used to secure the studs to the plate, or the bolt size and throw for a deadbolt lock. With thousands of pages of code and endless manufacturer installation requirements, one has to decide how much information are you going to include before your construction drawings become adequate enough to meet your "Designer / Architect Responsibilities" as stated in the code. -
Do conditioned unfinished basement rooms count as square footage
ValleyGuy replied to GeneDavis's topic in General Q & A
As far as permits here, the local counties make up their own rules. In my county, they treat permits like taxes - charge for everything then make up crap to gouge some more!! We pay for everything in the house, and for garages as well. However, garages do have a different sq ft rate than the house. Want to do anything over $10k, you need to pay for a permit - even if they will not be required to inspect anything. It's crazy, if you replace your flooring and it costs over $10k, you need to get a permit - the permit cost rate is based on the total expense of the job. We even need a permit to transport your baby barn shed if you want to take it with you when you move. On the positive side, there isn't much confusion whether or not you have to pay for a permit ..... only how much are you going to pay, and how long will the job be held up waiting to receive the permit. -
As @Renerabbitt has stated, its the wall layer direction. The wall layer direction not only plays a role in the label, but also if you have doors with handles only on one side. I have closet doors (ball catch type) with dummy handles only on the door exterior. To have it show properly in 3D as well as show properly in my schedules, the exterior of the door (with the handles) seems to always be on the exterior of the wall layers side - which makes sense.
-
Adjustable Space Planning Boxes. All of the Deck and Handrail / Newel upgrades. The multiple Schedule updates and abilities. Definitely upgrades and steps in the right direction. I haven't used all the new trinkets yet, but these are my favourites so far.
-
X16 Beta to Full Release, What is the procedure?
ValleyGuy replied to ValleyGuy's topic in General Q & A
Thanks Rene. -
X16 Beta to Full Release, What is the procedure?
ValleyGuy replied to ValleyGuy's topic in General Q & A
Thanks Rene, do I need to remove the X16 Beta first, or just instal and it will rewrite? -
I've never went from Beta to Full Release before. I'm currently using the Beta version and want to upgrade to the full release version. Do I just load the current X16 from the locker? Are there any unique steps involved to keep or save anything (files, etc...) from Beta? Thanks, Shayne
-
Here are the scale bars. It seems I have a very simplistic way of dealing with all the scale issues I read about. In my residential home construction world today, there is only one semi-important point, and one really important point when it comes to printing at scale. 1) I send all things that will be scaled to the layout in increments of what you would find on a scale ruler. This I found isn't really important to too many people as most now are only reading the measurements provided, or working off of a monitor with a cursor type tape measure. Most trades here don't want paper anymore, they just want digital plans sent to them, even the permit office and building suppliers. Putting things to the layout as per scale ruler sizing is more for my OCD and a few out in the field still using a tape on proper sized plans. I actually very rarely even supply any paper copies to my clients. ...times are a changing! 2) As I only use a layout sheet for 11x17 size, I always Export to PDF using: fit to paper at 100%. Everyone using a commonly found 11x17 printer can print the emailed PDF at 100% and it scales perfectly every time. The odd few that want bigger, print at 200% and get properly scaled 22"x34". I found that most of the digital world advancement messed up any control that I would have in putting the plans onto paper anyhow. Instead of trying to fight it, I decided to just include a scale bar to control things out on the job site. In the real world, different guys show up with all different sizes of plans with their own doodling and coffee stains, they don't care - they just use their cigarette package and a pen to make a distance that they want from the paper plan they have and hold it up to the scale bar to guess how long it is- easy peasy. All of the important technical measurements are included and any scale measuring is usually for estimating only. The scale bar isn't used that often, or even at all according to some guys. As far as how readable the the plans are, I have different saved dims and text layers for each SPV, Elevation, X-Section, CAD, Layer set... On my 27" monitor, a 11x17 piece of paper fits almost perfectly to my screen if my library is open and tool bars are present. So what I am looking at on the monitor is the same size of what the printed paper page will look like (at Drawing Scale: fit to page at 100%). If I can't read it on the monitor, I won't be able to read it on the paper - adjust as necessary.
-
I just made two different sized graphic scale bars, saved them into the library and put them on a tool bar for easy access. Scale bars are saved in all my plan SPV's and saved Elevation Cameras / X-sections. If any of these views get sent to the layout, the scale bars are just like a door or window and adjust to whatever the scale is used in sending the view out to the layout. I rarely need to add them as they always present with each saved view. They are on their own layer to toggle on or off as needed. 20 min of work once and they are forever there on every project, never lost, never at the wrong size, and rarely needing any workflow maintenance.
-
Corner to corner measurements: From a former foundation contractor's view point ... that plan shown has 25 corners and 3 T-walls .... I would thin down this SPV to just the concrete and would have about 15 corner to corner measurements! Concrete contractors will love and promote you like a king. This tiny bit of time on the computer is like gold when the homeowner talks with the trades... your plan value increases significantly and should leverage up you asking commission. @wesdutkaSteve and Joey are correct in my opinion, just show the wood wall on top of the concrete pony wall in the plan view (concrete thickness showing of course). As for not "...showing any of the other stuff on The Lower Floor Plan...", I use a "Basement Framing" saved plan view with a separate layer set line specifically for basement bearing walls and another for interior non-bearing walls to help display what I want and don't want to see. I also do not have interior bearing walls designated as "Foundation Wall" under the general panel in the wall specification (which automatically places a footing). Instead, I separately place strip footings on the foundation SPV and thus can separate footings and walls in each SPV for the interior bearing walls. After you create both saved plan views, create two separate layer sets to display what you want for each SPV. For each saved plan view you can then click on the edit active view icon and create all the different text, dims, arrow, CAD layer, Layer set, Ref display, etc.... When you have it the way you want, save it then go back and check off the "Never Save" option and it will lock in your choices. You have to remember to not arrow up and down when you want to see your "Foundation" and "Basement Framing" from any other SPV's, these are now very specific and need to be accessed from the Saved Plan View Control. Use the new layer in 3D for your foundation as well to get just your concrete. And if need be, use the Delete Surface tool to erase any wall layers that you don't want in your picture being sent to the layout. This is a little extra work, but far less than drawing another foundation and having two plans that aren't in sync with each other. You can also save this effort to your template for future use. On future houses, you could also start to keep every layer "in the dirt" as foundation (Level 0), and then start the walk out as Level 1. This will make your pony wall not on the foundation, but on the level that it is actually on.
-
Are we still not able in X16 to automatically frame a single 1-1/2" ledger board with a double 1-1/2" rim board on the other three sides of a deck, while having a bearing beam specified as the default? Or am I missing a selection box somewhere?
-
You could just use glass for the material of the doors and drawers.
- 1 reply
-
- 1
-
-
it never ceases to amaze me what some of you can do with a simple cabinet....
- 7 replies
-
- terrain
- elevation data
-
(and 1 more)
Tagged with:
-
I've done this before with placing a pass through (with frame and trims, w/o a label) in the wall with frame to fit wall checked. Build both windows separately w/o trims, w/ frame recessed 1" - uncheck fit to wall. Mull together and add the desired label. Center it in the pass through. It doesn't mull the mulled unit to the pass through, so you'll need to move both items, but it looks good.
-
You could try opening it up for specification and under the label tab, put a measurement in of how far you want to offset it.
-
@Gawdzira ahhh, I see what you are talking about now... good point. As Doug pointed out, it's probably a good idea to make a suggestion then. I guess I rarely see these two dims that close together because of maybe my work flow, dimension arrangement, and a little dumb luck. Work flow: I usually move walls into position using the temp dimensions while drawing, then apply the permanent dimensions afterwards. Dimension arrangement: a very large portion of my dimension lines are placed outside of the actual foot print -exterior wall dimensions, and intersecting interior wall dimensions. In your example, my temp dims are on the inside of the footprint and my permanent dims are on the outside-easily distinguishable. I do see what you are talking about with dims my dims completely inside. Maybe I just unknowingly made a habit to make the selection point on the wall far away from any permanent dimensions, thus keeping the temp dims separated..... ignorance is bliss sometimes. Thanks for bringing that to my attention... now I won't look at them the same way again.... it's like that noise in my truck that I never heard before my mechanic pointed it out and now I can't stop hearing it . You make a suggestion, I'll support you on it.
-
I don't think I have ever seen two temp dimensions like you have. Not sure what is different or where else to look other than the defaults.
-
Need help getting a materials list made the way my boss wants.
ValleyGuy replied to DarrenWHatch's topic in General Q & A
I totally agree with Rene, you will spend endless hours fussing with a plan when an experienced guy with a piece of paper and a pencil could have an even better and more complete take off done much much sooner. Each house can be built in many different configurations and with many different material products that all have specific consequences in regards to the material takeoff list. Unless your company only builds one specific wall configuration, you may end up with many, many, many different wall types with many different macros. Chief doesn't draw caulking, tape, wind bracing, fasteners, .... the stuff that changes significantly just by changing the layer order of a wall. Your code requirements may need to be accounted for in the macros as well because of something as simple as reversing the foam and OSB layers, or placing and opening too close to a wall corner. I can't even imagine the time that you will need to spend maintaining your 'macro system' as products, install techniques and building codes all change and adapt. CA comes up with new features year after year that may affect them too. Heck, I can't even imagine how much time and effort you will need to invest to learn about macros in CA to get a good enough handle to write or maintain them properly at that level. After working in a building supply business, take offs are much easier, faster and more accurately done outside of CA than using CA. I'd use CA to provide information like surface area and as DBCooper suggested, manipulate the material / buy list to help out with some of the numbers. After going down this path in CA at the start, I humbly admit that I wasted a lot of time. -
Steve does this mean you and I won't be able to RT with our iMac's? I'm not well versed in computer logistics, I just hope the thing works when I turn it on in the morning lol. This machine still gets me from point A to point B well enough, so you won't be breaking my heart saying that my iMac won't do it. I agree, it is nice to see CA putting in some hard work for us Mac users, thank you CA.
-
You are welcome. I don't have any other programs that I use the space mouse on so I have nothing to compare it to in that regard. I understand the "no joy" a bit, I did almost send the thing back at the start because I was having so many problems with very little set up help offered at the start. Even the instructions manual is geared toward PC equipment. The joystick freezing up when both mice are moving at the same time is a bit frustrating, but getting more tolerable the more disciplined I get at completely letting go of my roller ball mouse. Thank goodness exiting CA and re launching it only takes 20 seconds. I really only use the joystick in plan view while building the model, and a few times I built the whole house without using the joystick at all. I like how the joystick really excels when doing a customer walk-through though, where I have very little roller ball mouse interference grief. It's the buttons that I really appreciate the most and I'm trying to keep the mind frame as I do with all the other tools I work with ... it is what it is and does only what it does. So I try and minimize the self-inflicted frustrations. Good luck with giving it a second chance.
-
You are quite welcome Lisa, I'm glad that I could help while also sparking a memory of yesteryears. I'm not exactly sure how the MacBook is with the 3D mouse as I have an iMac, but I suspect that it should work the same. I wonder if the MacBook with additional exterior monitors may be an issue as I've heard of a couple of people having tool bar issues - both on MacBooks. Good luck with it, and hopefully Christmas comes early for you.
-
We do these all the time here, and I struggled with this for quite a while too. This works for me, you might want to tinker with it to get your appropriate thicknesses, heights, etc to fit your needs.