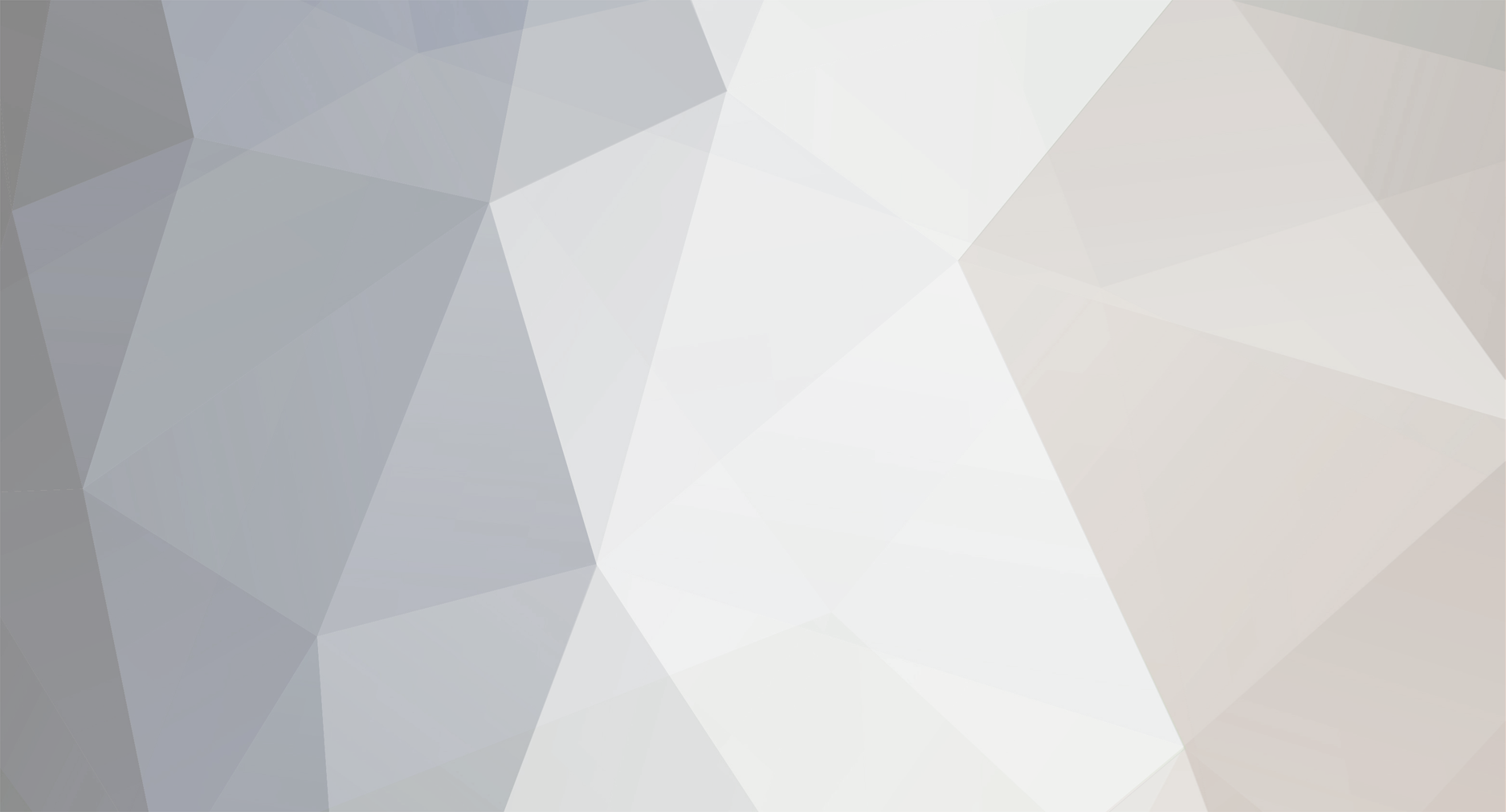
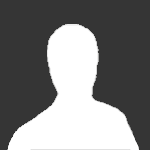
ValleyGuy
Members-
Posts
318 -
Joined
-
Last visited
Content Type
Profiles
Forums
Gallery
Everything posted by ValleyGuy
-
I agree, that Apple mouse is really only good for surfing the web or tasks involving little accuracy. I really enjoy using the MX Ergo S Plus roller-ball mouse from Logitech. For $140 CDN ( ... about $1.98 USD lol) it has 6 programable buttons and speed control for the curser. It is cordless, rechargeable, and has a roller wheel for zooming in and out. It's well worth it to invest in a good CAD mouse.
-
Good point, I'm pretty sure that my Mac Intel system will not support X17. So until I upgrade my computer, I'm stuck at X16. I also agree with other's request for more meat and potatoes. I'd be in favour of a version or two cleaning up and bettering some of the already established things in Chief, instead of starting new projects that will be added to the list of things needing some help and refinement. There are items in life that I purchase just because 'they work as they should' - not pretty looking, but robust and reliable. Get the job done efficiently type tools. Tech seems to always be expanding, but we are in a business type market that requires productivity needs over flashy extras. Somewhere CA tech will expand it's envelope far beyond what is really needed to get the job done and more people will say that they really don't need to upgrade. Maybe it is becoming more of a case of what do we want this program to do? Is CA spreading itself thin in some areas by trying to add in all the new tech advancements? I stopped buying new cell phones for similar reasons. I just want it to keep a contact list and make a reliable call (that stays on the phone and not suddenly jump to the truck) ... it is a phone after all. A lot of the flashy other things seem to become insignificant when I am trying to use the phone .....as a phone.
-
There seems to be two main paths to reporting SF information, basically because of the way the SF information is obtained. CA will split the walls between adjoining rooms, ex: the garage and house through wall will be divided evenly between the house SF and the garage SF (the same idea inside the house envelope, bath to bedroom,...). Some people are fine with this and some people are not. 1) If you are fine with it, you can use a macro in any one of the room's Object Information listings (code, comment, description, ...) and make a schedule to report that information. 2) If you are not fine with it, then the poly line method is another option. I use both methods for different schedules as well as a few macros to differentiate between New and Reno rooms, you can get as deep down the rabbit hole as you like / are able. Here is my method to accomplish both ways: 1) Room Reporting the Area: I programmed all of my room types to have a macro in the description. Room -> Object Info -> Description -> insert macro -> Global -> Room Info -> Standard Room Area. I then include the column 'Description' in my SF schedule (change the Description label to whatever you like). You can customize the schedule to include, or not, whatever room you like. It's dynamic and doesn't usually need any edits. NOTE: Making each new room retain the macro; there isn't an OIP (object information panel) in Room Defaults (little wrench) to add in the macro under description. To get around this I deleted all but one of the OOB room types. I made a room (in my template plan) as it does have an OIP, open up the room and insert the Standard Room Area macro in the description (I also added the Room Name macro in the comment and have the comment column in my schedule), and adjust all the data to fit the room; name, conditioned or not, flooring, schedule, ... While the room is still open, go back to General -> Room Type -> Define -> Copy. You can now change names and data as needed for every room you create. Save your template and you will retain all that information. 2) Poly Lines: I made a saved plan view and layer set for my p-lines in my template. They live there with all the programmed info, (macros, labels, colours, ....) and report to text box saved on a CAD sheet. The text box is my schedule and lists the info I want to report. The only real maintenance is to size the p-lines as you are doing now. I saved the CAD sheet on my layout, however, it needs a poke to properly activate - open and close a p-line (just one on the SPV) and open and close the text box on the CAD sheet. This will activate the p-line data and activate the calc's in the text box to show the proper numbers. I'm fairly new at using them too and can't stray too far into the deep end yet, so I'm sure there are lots of variations of how to accomplish little to no maintenance in streamlining the p-line task.
-
I used to import all of my freshly made wall types into my template, and just like Michael stated above... there becomes a lot of them. The interior walls are pretty consistent, it's the exterior walls that really seem to add up for me. The problem that occurred was I had a really long list to scroll through when in the wall specifications choosing a 'wall type'. I like to be able to control the plan view wall layers look and maintain control on all of the many different layer sets for all of the different walls created. I also like to have an accurate and dynamic wall schedule (exterior 6" wasn't quite cutting it). The same house may have many 'exterior' walls; walk-out basement walls, main floor walls, garage walls, garage to house through walls, second floor walls, dormer 'ghost' walls, attic to living space walls, attic to exterior walls. A lot of these you may want different wall component for, or different plan view looks, all for the same house. Some even take advantage of the new 'display layer' under the wall type for even finer control. Add this to the many different houses and the list gets exhausting. So I started putting them into my library under specific 'Wall Sets'. My library is always current and always on every plan... no need to chase after old plans to find the walls to import / copy. To get each of the specific library saved walls into the plan, just select the library saved wall and use it like the regular wall tool. I don't think that I really go into the 'wall type specification' list any more and it stays as a short list for each new template that I open. If I make a new wall (or set), I can immediately save them to the library and do not need to update my template plan but keep on working. I really like having specific house type walls grouped and in the library. Once that group is opened, all of that house's walls are on display just like a drop down list of wall tools. Another bonus is specific wall data is saved for each specific wall; whatever info you want to save only has to be created once. If I want a specific wall to be framed with a specific material so it stands out in a camera view, have horizontal girts of a specific size, specific macros attached, or I want the specific wall layer description in my dynamic wall schedule to be accurate, it's all there. Just remember that if you want to change a wall already drawn, don't just open up the existing wall and change the wall type as that will be the only data that you are changing. The description, layer, etc will stay the same. Draw over top with the new wall. I'm sure there are many ways and systems to accomplish this task, this one seems to work well for me.
-
As everyone above has said above, SPV's are really useful. Your team has already completed most of the heavy work by creating the different layer sets. SPV's just streamlines the process to maximize efficiency and organization with an extra hint of consistency, plus a measure of safety for errors and omissions. Here are just a few things to think about... Efficiency: - one click to change a lot of things; floor level, active view defaults, active dimensions, active layer set .... also, reference display. This is a big one for me, ref. disp. has it's own floor, layer set (colour, line weight, displayed items, etc), and stacking order, is saved in a SPV, otherwise one ref disp layer set will have to do all floor levels. - no time wasted sending any plan views to the layout. Each SPV is already saved on the layout and as soon as the layout is linked to the plan file, all plans views are updated instantly. Plus they remain active and current. - save time deleting errors because you forgot to change the active view and now you have the wrong sized text or the wrong note symbol... populating the wrong note schedule. Ever forgot to change the active dimensions or the layer set and now it asks if you want to display that layer because it isn't turned on... just one more pop up window to deal with before you draw the exact same dimension for the second time. Organized: - not all SPV's are for the layout. Overwhelming the customer shouldn't come from them watching the mouse do multiple clicks just to check a measurement or put a note onto the proper schedule, adjust the text size, or scroll down the long list of Layer sets. Professionalism is sometimes viewed by flow, rhythm and being organized. - If you have saved camera views to help save time and keep you organized, SPV's are very similar and just need to be set up and saved. This is my current SPV list, the "A" numbered ones are saved to the layout already and the ones w/o the "A" are for working / customer related reasons. Only the working / customer SPV's share the Active Defaults between floor levels and are arrowed up and down.
-
You got it, I have a Note Schedule on the CAD sheet that I send to the Layout as needed. The 'dumb' call outs are just CAD blocks.
-
2) consistent notes: This might help for plan Notes. I use a Note schedule on a CAD sheet saved in my template. I just add the note to the CAD sheet off to the side of the schedule (to be clipped out of the layout picture). I created 10" symbols and added them to my library. I use these library symbols to cover the symbol on the schedule (to keep both the schedule and plan looking consistent) as well as drop them into the plan as required. The schedule of notes will be the same every time this template is used or copied and the library symbols can be dropped into the adjusted / mirrored plan view as required. Save the CAD sheet in your Lay out template and you should be set. I have red hexagon and blue pentagon symbols for other note schedules.
-
Save one of the adjusted items from your plan to your library. Then choose the item from your user library to put into your plan and it will retain all the adjusted information. You can even change the name and anything else as required of your new user library item.
- 1 reply
-
- 1
-
-
I'm planning to upgrade to multiple monitor displays and can't seem to see anything specific to CA as to what actually is visible and how things interact. I've never used multiple monitors ever, so I really have no idea what to expect from Chief. I'm hoping that others already using multiple displays will share how things work and maybe some pictures of their set up / screen images. I am looking at having 3x 27" mac displays to match a mac computer, so everything will be compatible. Please keep your wise cracks to a minimum about Apple vs PC, the idea, regardless of which system is used, is focussed on what needs to happen on the screens when specifically using Chief, and see some good useable monitor configurations - side by side monitors, stacked monitors, one landscape and one portrait, different sized monitors, different combos....maybe should I be looking at something different than 3x 27"?? There is lots on the web for video, photography, coding, gaming, web browsing set ups, but what really is working for Chief users? What is actually dragged to the additional screen? Is the whole program (what's visible on the screen) or is it only part of the Chief program (such as only the layout)? Do the tool bars need to be adjusted? (for example; if I have plan view on the main monitor, 3D and elevations and library on a second monitor, and then the layout on the third monitor.... do I need to jump back to the main monitor to use the associated tools? I have different toolbar configurations for different views and of course they are different between the plan and the layout. If toolbars need to be moved over as well, how is that done and what does that look like? Maybe the associated toolbars just populate on the other screens? Maybe I need to have tool bar consistency? Are there any other things that I should be aware of using multiple displays? Any help would be greatly appreciated, thanks.
-
I used to sell wood to our local military base for target practice, it had to be clear pine. This was to minimize ricochet on an open air range. If you needed to use wood framing, maybe knotless would be best?? An idea about design: I'm not sure if the lot would accommodate, but you might consider having the range jut out from the main structure to be a shaft into a hill, like a separate 'wing'. Concrete on 5 sides surrounded by earth, just the one end attached to the house for access - still part of the house (basement) but minimize the danger.
-
Hey @winterdd, perfect timing... my new code books just showed up today... and yup, nothing yet about guns in the Canadian Building Code either that I could find lol... A couple of local-to-you places may offer some insight of the logistics, 1) you probably already checked with a gun store close by that knows of someone that has an in-house range. 2) check with any other businesses that require an explosion room. I remember the city bus barns (of all places) that needed to install an explosion proof room to store the shop explosive items (and yes, from experience, gas cylinders really do act like missiles under the right conditions...). The specs might be different, but the logistics and legal requirements may be similar. Around here, people just slide open the window and shoot at the squirrels and crows from the kitchen... where they can't see you coming .... This is a cool one, keep us posted.
-
You could try removing the curbs from the road and converting CAD lines into mouldings. I made mouldings and put them into my library. Mouldings allow you to mess around with the height and widths as well as the offsets. It's fairly easy to have a proper looking driveway entrance. With a little more fiddling around, I'm sure the sloped cutaway could be achieved, maybe a 3D solid??
-
What is the best way to create a series of plans?
ValleyGuy replied to martinconst's topic in General Q & A
It might just be a Mac thing, I'm not sure what options are on a PC. Maybe someone else could answer this for you??? -
What is the best way to create a series of plans?
ValleyGuy replied to martinconst's topic in General Q & A
The 'Archive' folder I have listed is used differently than the CA Archive. I use the CA Archive files as @GeneDavis is showing as more how you described, a computer crash back up that 'Auto saves' every few minutes as per my set up default. My 'Archive' folder holds the plan and layout that is duplicated every time the client wants a change/revision throughout the process of completing the initial construction documents. Some of the benefits that I have seen: 1)I can have the current version in front of the customer making changes, and have the last version (plan, cameras, measurements, etc,) as a second plan opened for a reference. 2) I can tell exactly what revisions we discussed on what day. 3) I get feed back from the time log and the revision notes attached - this helps with gauging meeting lengths vs work vs billing. 4) I always have a solid plan that I can fall back on to have a fresh start with incase I mess something up while sitting with the client making changes. There are others, but these are the main ones. I'm a one man band so it's all purely selfish how I set up my files and I'm sure this system wouldn't work for some. Everyone has their own system, it's just my current way of filing things. -
If you are looking to just 'not include' the revision notes in the layout PDF, couldn't you just turn off all of the revision notes for all SPV's using the "Modify All Layer Sets" in one fail swoop? They wouldn't then show up in the layout. As for deleting them all, I don't think that there is a global way to do it.
-
What is the best way to create a series of plans?
ValleyGuy replied to martinconst's topic in General Q & A
I just did one in November and did it very similar to how @Alaskan_Son said above. Once I completed one whole plan and layout (with saved camera views), I just saved and closed both, went to the file directory and duplicated a new folder, then renamed it. Open up that plan, adjust as necessary, then open the new layout and relink to the new plan - both are in the same folder and play nicely. Rinse and repeat.... -
Thanks @MarkMc I've never used that button before, then again I have each CAD type saved with each SPV so I rarely ever change CAD on the same plan view. Good to know though.
-
This also works! Thanks Michael
-
Thank you @glennw, sounds so straight forward when someone else says it!
-
I tried both of those ideas, unfortunately neither worked. Over top just pushes the lower one away to open up a fresh clean space. Dragging outside and releasing just lets me see it zoom back into position again. RH click doesn't do anything. I'm really at a loss. Thanks though.
-
When you make a CAD line it will have a default layer (CAD, Framing in your example). If you open up the CAD line, there will be a heading on the left "Line Style", you should be able to change the Layer, Colour, Style, and Weight. Just designate it to the "CAD, Hidden" or whatever you have called it. If you are wanting to just use the CAD tools and have the line automatically default to your newly made "CAD, Hidden" layer, that is a different thing altogether. You will need to got to the Project Browser and choose the Plan View > (Right Click) Edit View > Selected Defaults > Layers > Current CAD Layer > Define > un-check CAD, Framing and check CAD, Hidden. This (along with the colour, line style and text style) will now make the default layer when you use the CAD tools follow the "CAD,Hidden" layer. You can switch the default back and forth by doing this through the Project Browser as needed.
-
Does anyone have an idea how to delete these once they are added?
-
I've used a few of them, not really all that popular due to price. They are exceptionally useful for egress below grade where there is minimal window well space on the outside. I've also put them in for pass-throughs from the kitchen to the patio eating bar on the outside of the wall - the full glass matches the rest of the house casements but doesn't knock everything off the bar. I can get them in a single side swing or both sides swinging (I think it is called French Tilt & Turn). There are even Tilt / Turn and Tilt /Sliding Doors.
- 11 replies
-
- 1
-