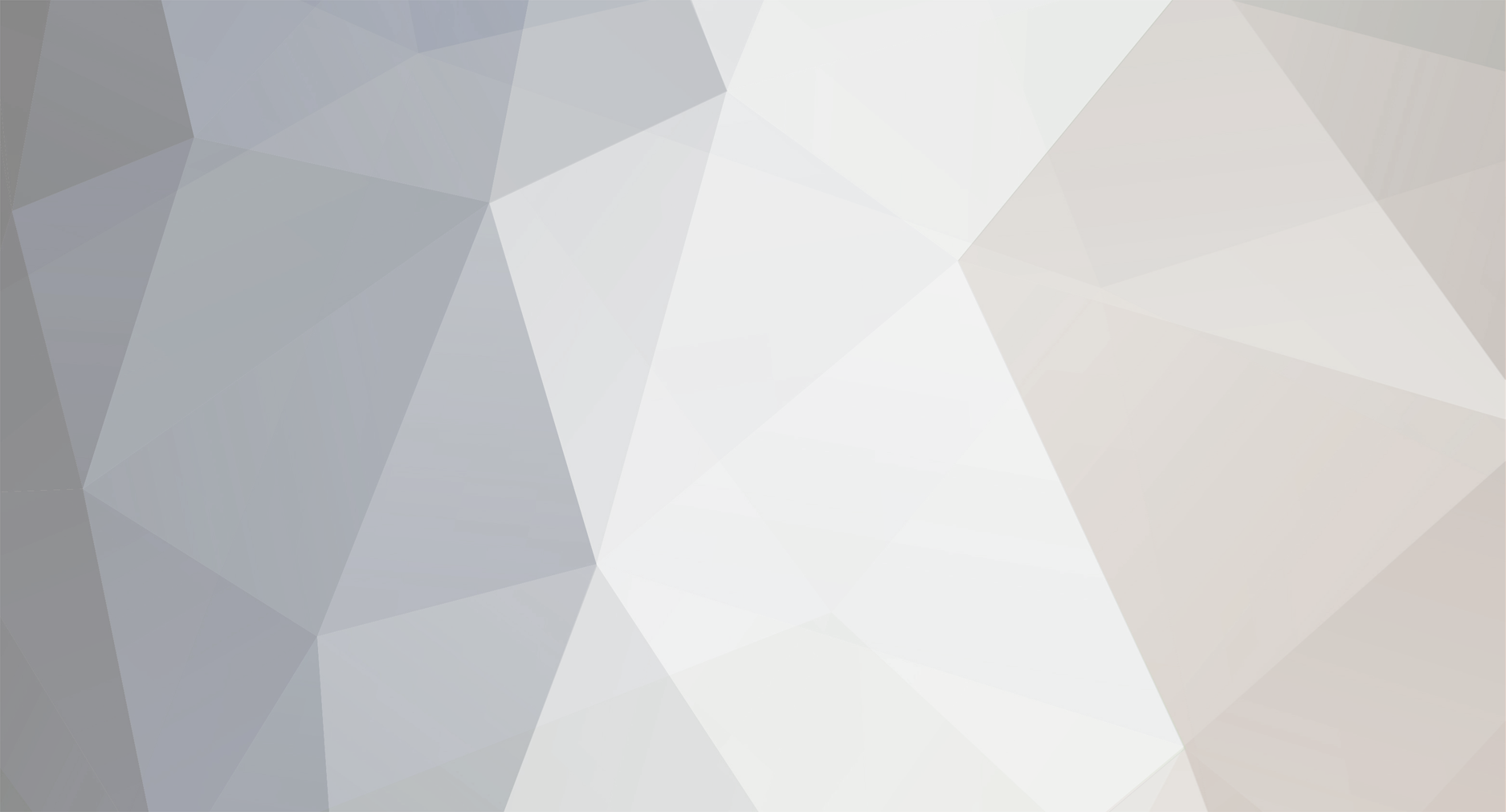
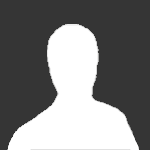
ValleyGuy
Members-
Posts
321 -
Joined
-
Last visited
Content Type
Profiles
Forums
Gallery
Everything posted by ValleyGuy
-
When you make a CAD line it will have a default layer (CAD, Framing in your example). If you open up the CAD line, there will be a heading on the left "Line Style", you should be able to change the Layer, Colour, Style, and Weight. Just designate it to the "CAD, Hidden" or whatever you have called it. If you are wanting to just use the CAD tools and have the line automatically default to your newly made "CAD, Hidden" layer, that is a different thing altogether. You will need to got to the Project Browser and choose the Plan View > (Right Click) Edit View > Selected Defaults > Layers > Current CAD Layer > Define > un-check CAD, Framing and check CAD, Hidden. This (along with the colour, line style and text style) will now make the default layer when you use the CAD tools follow the "CAD,Hidden" layer. You can switch the default back and forth by doing this through the Project Browser as needed.
-
Does anyone have an idea how to delete these once they are added?
-
I've used a few of them, not really all that popular due to price. They are exceptionally useful for egress below grade where there is minimal window well space on the outside. I've also put them in for pass-throughs from the kitchen to the patio eating bar on the outside of the wall - the full glass matches the rest of the house casements but doesn't knock everything off the bar. I can get them in a single side swing or both sides swinging (I think it is called French Tilt & Turn). There are even Tilt / Turn and Tilt /Sliding Doors.
- 11 replies
-
- 1
-
-
The materials list in Chief can actually produce very detailed and specific lists, but like I said, it takes a lot of work. If Chief put some more effort into connecting the room name in the poly line, then it might eliminate a lot of this work needed to produce a good material list. I did a little mock up room similar to yours and came up with a few more items on the list. I am not aware of a neat way to isolate just the LDY room items. Here are a few things that you will need to consider if you want to keep on going with it: 1) Many different walls with many different individual layers, all making the distinctions between rooms. Thats how to get individual sides of each wall. Many different materials for many different rooms. You may want to use style palettes to spray rooms, and group save walls in the library. You could minimize some of the work by minimizing the number of layers. 2) Individually adjust every single wall's components (ie: I opened up a wall > Components --- Green Board Walls LDY > Code --- typed in "LDY".... then move to Drywall Main Floor > Code ---- typed in "Bed #1"..... the same for paint on green board, paint on drywall, primer on green board, primer on drywall, VB, insulation and anything else making up that specific wall. The amount of work is tied to how much you want to separate out. I used many different wall layers here, but it could be thinned down to just include drywall. 3) Make sure that all of your materials are measuring how you want them to read (ie 4x8 sheets or 54"x12' or sqft area or LFT...) 4)Make sure that the individual components are under the appropriate ID. The material list is driven by ID labels such as Flooring, Insulation, Wall Board,... Having the wall vapour barrier in the wall board ID and the paint in the framing ID will make your material list a mess to read. Also, if you don't report framing on the material list and some drywall is mistakenly in the framing ID, you will never know about it. 5) Put your material list in an order to easily read. Also do the usual stuff like making columns appropriate sizes (in the actual list) and eliminating unwanted columns (in Preferences). Just start messing around with the material list, you may find ways to customize it better toward your needs. Good luck with it.
-
Yes I totally agree that it would be nice if they could do a little work on it to provide the wall surface area too. You may want to check out this earlier thread, it may give you a little more info on how to get individual sides of drywall to show in the materials list.
-
If this room is all that you are trying to calculate for, manually estimating is by far the easiest, quickest, and the best sheet size optimizing way. I see five walls that drywall would possibly be best if stood upright, a window and a door opening. There is going to be waste and it needs to be accounted for. Drywall comes in different widths and lengths and can be ordered to save unnecessary waste. As the program will either give you a wall sqft area, or number of sheets based off of that sqft, you are most likely going to get less than pleasing real world board count numbers (I'm not sure that two different board size measurements are even possible in a single material specification on Chief). For example, it would be silly to have the materials list give you a 4'x8' sheet count for a 9'6" x 9'10" room. It's much easier to say 7-10's and 4-8's will cover the walls, with 3-10's for the ceiling. However, you will need to adjust accordingly if you are wanting green board and it only comes in 4x8 sheets. Or maybe you have 9 ft ceilings and want 54" wide drywall that your supplier only stocks in 12's. Or maybe you have 10' ceilings and you will want to stand all the drywall upright and therefore only order 10' sheets. Maybe there are physical barriers (like stair headroom clearances and hallway corners) that only allow you to use a specific size board. As you can see, you will have different sqft totals, different amounts of waste, and different board counts all for the same room, just because of different real world scenarios. What you are trying to accomplish is somewhat possible in the materials list a couple different ways, albeit a different approach than just using the poly line. It will definitely take a lot more effort vs adding up the sheets manually for this tiny room. Material lists are sometimes still best done old school for optimal real world results. If you are still wanting to forge ahead with getting Chief to give you a number in the materials list: the easiest way is to probably make two different wall types for the two different walls that you have (2x6 and 2x4) making up this room. Make the wall layer on one side have a new material for the drywall, call it something different (like 'laundry room drywall' ) and give it a specific wall layer colour to show up in plan view. Replace the original walls you have shown with the newly made walls making sure that the new 'laundry room drywall' material layer is inside the room. Make a new materials list and look for the new 'laundry room drywall' - you may need to delete other items from those specific walls that you may not want like studs and drywall from the other side.
-
I send the elevation to layout as a live view - 'update on demand', then go to the layout and open up the view and change it to plot lines and make the line weight thinner (1 instead of 18). Only because I want to adjust the default line weight and the only place to adjust the line weight is to open up the layout view. You could send the elevation to layout as plot lines, the lines will be whatever your default line weight is. You have to go to the layout and open up the view to see what your default line weight is then adjust to what you would like. If you make adjustments to an object back in the elevation, then you would need to update the layout view. There will be a prompt before closing out the elevation to ask if you want to update the layout (you can always go to the layout and refresh as well). Yes, changes / additions to text and dimensions in the elevation will be dynamic and not need the layout view to be manually updated. They just appear on the layout and are always current. The plot line weight just comes in at a default that is quite heavy, mine is 18. From another thread from a while ago, no one seems to be able to adjust the default value now that Chief took away that option. I don't like the 18 weight so I adjust it to 1.
-
@kwhitt DB and Joey are correct, plot lines is the way to do this. All cameras will work as far as I know, and the plot plan view keep dimensions live. I don't like to bog down my computer with constantly updating the layout, plus CA decided to drop the line weight adjustment option in the 'send to layout' pop up window a few years back.... so I always send the camera elevation to the layout as 'update on demand'. Then in the layout I open up the view and check the plot lines and adjust the line weights. This only gives plot lines, so textures don't work and glass house goes to plot lines, however, depth cue does work nicely. If you leave the layout box boarders larger, Text, Rich Text and Dimensions are live and show up automatically when added to the plan elevation with no updating required on the layout. If there was a way to set the default line weights (like it was before), without having to do this step manually in every layout box......
-
I had this happen to me before too. Just changing your floor height in the basement back to -118 5/8" should fix you up (you will need to put the 60" ceiling ht again, but the -118 5/8 should stick). I noticed that even a change in the floor finish didn't 'erase' when I deleted the walls and then started over. I'm not sure about this room memory thing that Chief has.
-
Happy 20 Years as Chief Architect !
-
Is there any solution to stop this 'room' spilling outside of the foundation pony wall? I would like to stop the floor surface at the inside of the wall. There is a wall specification to stop the sub-floor at the inside of the wall, but I can't seem to find anything to control the floor finish. Any ideas???
-
It appears that you have one truss off of the house fouling things up. I also see that you have a ridge board. Try deleting all the roof / truss framing.... Edit > Delete Objects > pick roof framing / trusses / rafters for this floor. Manually delete any ceiling planes over the deck. Manually delete the roof planes over the deck and the associated main house single roof plane. Shift select the two side railings on the deck and open them up. These should be room defining and under the rail panel, choose 'Rail to Beam'. I don't think that it will work without this. Open the deck room and make sure that the roof over room is selected and the flat ceiling is not, which you probably already have done. Make sure Auto Roof (check Trusses box) and Auto Roof Framing is on. This should make your main roof and your covered deck roof look like my first picture above. Shift select the two roof planes on the deck and make sure that 'trusses' are selected under the general panel. In the structural panel make sure to uncheck 'Ridge' and 'Lookout'. Pull the main roof peak point to the soffit - make sure that it is properly aligned with the soffit. It won't work properly if the points aren't snapped together to make a straight line. The roof planes won't really re-build other than make a rectangle again, but it will produce the truss base and add the valley truss framing. You should see a pop up warning saying... it modifies.... Do you want to proceed? Yes you do. Follow with the rest of the above directions adding in the three new ceiling planes and Bob's your Uncle. If you pull an elevation and spilt your screen to see both, you can witness the growth of the scissor truss with each ceiling plane that you put in. If you pull a complete framing overview and see that you have a rogue truss extending through from the main house into the covered deck again, you likely have an issue that someone will need to look at your plan to solve.
-
Pulling the roof plane on the main house (peak point to soffit) should change the direction and create a truss base for you. Then make three ceiling planes over the deck with the centre one flat should make the scissor truss. Everything was done on auto roof and auto frame except the material and colour change at the end (to show better in the pictures). Hope this helps.
-
You will need to change the direction of the trusses. You will most likely also want to build a truss base over the other roof to support your valley trusses??? There are good videos in the training video library dealing with the roof, it's defaults, and the framing. You can access the videos through your dashboard > search roof. Lots of good info, check them out.
-
Auto Exterior Dimensions - Interior Walls
ValleyGuy replied to ComputerMaster86's topic in General Q & A
Disclaimer: I tend to dimension as one would frame.... only exterior walls with associated openings, plus interior bearing walls (in Red) on one dimension line. Then a fresh dimension line (in blue) for a fresh start when the interior framing begins. Less confusion as the bearing structure framer does not need to know (or want to add up) the interior divider wall measurements. Likewise, the interior framer does not need the measurements for the front door or a window opening when framing inside walls as that framing is already completed. Adding a 0" line to your main wall layer (exterior side) may help you achieve what you are after. -
ICF Walls, wood top plate, trusses on top. How?
ValleyGuy replied to ByronVallis1's topic in General Q & A
I happen to be working on one right now. Just make a pony wall with the upper wall 1.5" lower than your wall height. Mine is on the second floor so that is why my elevation of lower wall top is so high. -
Those 'southern' boys have a good way .... if you don't need to deal with frost protection lol. No wise cracks about Canada, I actually on the same latitude as Old Faithful in Yellowstone. @kimberlywilson you will find many different ways to do things in Chief, all come with pros and cons. Porches are no different. I draw my "concrete slab porch" rooms using invisible room divider walls (floor elevation -2"in this case to show below the door, no floor or structure), then add posts and beams as required. Jump down to the foundation level to add in the foundation (sono tubes in this case), back to the main level to finally add in the concrete slab (at -2" from absolute to match the room). Here are a few different things offered with this method: 1) I split this exampled bi-directional porch into two porch rooms. This allows the wood soffit to change direction with no worry about the associated railing or patterned concrete mismatching. 2) The concrete slab is a separate item that can be whatever shape needed without disturbing the porch room, placed at what ever elevation height you want. If there were stone bases on the wood posts, you can easily make the concrete to fit the pillars properly. If you had patterned concrete and it was sized beyond the room, the pattern isn't interrupted. Maybe you want a different coloured and patterned border around your concrete slab, just make two (or multiple if you want) - concrete isn't always just gray. A second option is the slab does not have to be a 3D solid but could be a landscape item. This allows for terrain sloping, as slabs do in the real world. Nothing like a 3D solid slab sticking up too high above the terrain, or worse - having grass growing through one corner then having to mess with the terrain elevations. 3) Separate beams and posts can be placed on different layer lines in layer sets. More control for each view (line weights, colours, draw order, display, labels) 4) Posts can be adjusted without opening anything in elevations or 3D views - select it and adjust the top and bottom height edit handles. 4) If you want a 6x6PT post and a PVC post wrap to show on a materials list in different listings (framing vs trim), you can with separate items. 5) Foundation items will show on the foundation level.
-
It's greatly appreciated that CA is putting some good effort towards schedules, that's for sure. Did you ever find out how the other programs handle this total sqft issue?
-
Anyone using a Mac Mini M4 or M4Pro with x16?
ValleyGuy replied to jgriesshaber's topic in General Q & A
@DawnSimp there is one option from Apple that you may want to consider, Nano-Texture Display. I have it on my iMac and I love how it basically eliminates almost all glare. Sunlight through house windows when at a clients home is no problem at all, even if they are sitting on an angle to the screen. Well worth the price in my humble opinion. -
I just keep all of the CAD poly line boxes on my Terrain Working SPV. I just cut and paste to the upper and lower floors - then back again to the home base parked off to the side. I'm barely out of the staring blocks on macros so there isn't much depth of experience to draw from.
-
I exhausted everything I knew to get a total from a schedule and came up short. You are right about the different poly lines on different layers / multiple plans messing up the numbers. I scratched my head and said a few bad words until I figured that out.
-
It isn't from a separate schedule. The individual floor values come from CAD poly lines with a macro in the label. The total is a macro formula in a Rich Text box.
-
There is hope with schedules..... after a tough couple of days of trial and error, I think I have beat this thing into submission. I'm no wizard with macros, but I did scrounge enough information to make a few that I needed. I also did some creative work with the X16 schedule abilities with macros already supplied. It is mostly dynamic and only a few CAD poly lines and a couple of text schedules that need to be poked to update. Maybe this will encourage those that want to learn some basics to take the leap. It really was a good learning experience.
-
How to get wall layers to extend above ceiling finish
ValleyGuy replied to Bergie3941's topic in General Q & A
Gene I have asked the help desk on this subject and they could not help. Around here, the rafter bottoms are strapped out with 1x4's then the ceiling drywall is attached to the strapping. With the strapping actually being part of the ceiling layers, every one of my plans has a 3/4" void where there is an open above situation (stairs and vaults). When needed, I have just resorted to filling in the gap with a 1/2" solid pretending to be drywall. -
How do I get this closed riser/open below look?
ValleyGuy replied to Kalvin18's topic in General Q & A
This may be close enough, make your treads with 0 overhang and about 16" thick, open risers and open underneath.