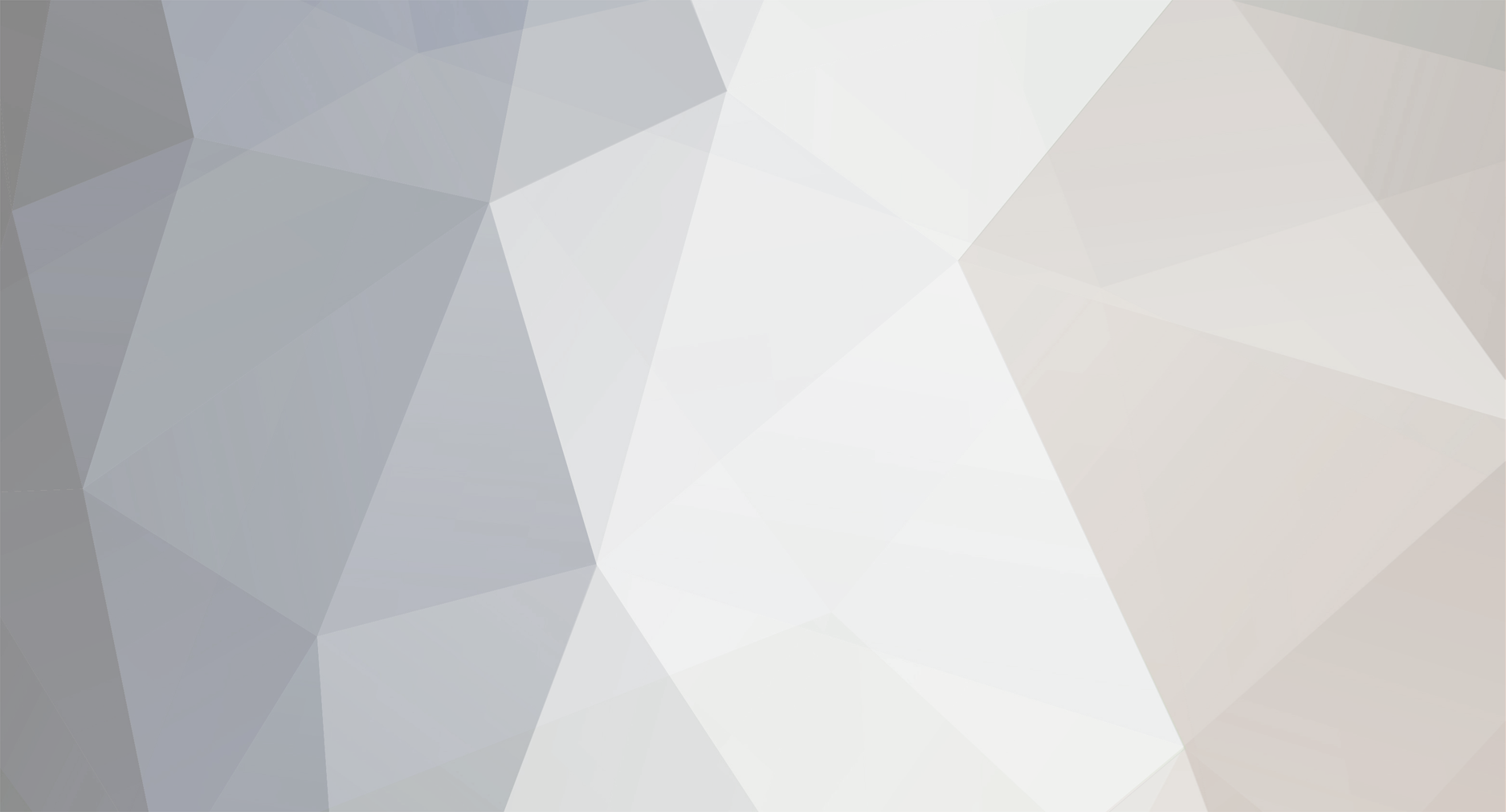
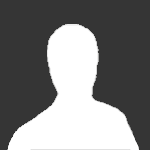
RodCole
Members-
Posts
626 -
Joined
-
Last visited
Content Type
Profiles
Forums
Gallery
Everything posted by RodCole
-
wall framing Dividing Wall Framing for smaller unit
RodCole replied to boxerprod's topic in General Q & A
This is from memory, but from what I am remembering the key is that you need to make a copy of a wall type and rename it. It can be the exact same configuration, but it must have a new name. Using wall labels helps to keep things organized. I did this on a room by room basis on long exterior wall of a hotel building. It worked out fine. It has been over a year since I did this, so you might check with tech support if you have any issues. Hope this was helpful. -
Looking for Models and Material List Creation
RodCole replied to HDReynolds's topic in Seeking Services
BIM Model is an acronym for Building Information Model. What that actually means is a bit harder to explain. In reality a 2D CAD file that has CAD Blocks with Data assigned as attributes that can be extracted and imported into either a data base or excel qualifies. But what is generally expected these days is a 3D model that could include a number of material and scheduling capabilities. I do this type of work on commercial projects, and much of what needs to be provided depends on what software the client or others involved in the project are using and what their needs are. In this case I would expect they would want a chief plan file that could be used for project management, and a list of building materials as requested. -
Ridge_Runner, Easy CAD was my first CAD program too. I ended up using AutoCAD 12 and Chief because FastCADs 3D modeling tools could not do the things I could do with AutoCAD Solids. I now use TurboCAD Pro Platinum for my more complicated solid modeling work.
-
Version 2. From what I remember roofs did not come out until version 3. I used to use FastCAD 3D for roofs. I did not have any formal training, but I did buy a video from Chief that was done by Dan.
-
You can also apply an Alpha Numeric code in front of any existing layer, or newly created layer. This method is a lot of work, but it does have advantages in organizing by Discipline and sub categories. Where it becomes more worthwhile is when you are working with other programs and want to keep things more easily managed between the programs. Layer filters can also work to display parts of more than one grouping if your codes are set up for that, and you use the right key combinations when filtering. An example of this is, say you want to view layers for both Architectural elements of the model related to only roofs as well as the related framing layers and nothing else in order to keep your layer list more manageable. Again, this method is a lot of work, but it does have advantages that Chiefs OOB alphabetical only arrangement does not. If you want to try this out I would suggest copying the layers into excel, renaming, and copying them back. I like this method because it lets you test out the sorting before changing any of Chiefs layers. BTW, use a test plan until you have it ready for prime time. You can also play around with the suggestion above, add a numeric code after the main category. Also spaces can place a layer ahead of others as well. This is a lot easier to start with.
-
I use Blender for the file conversions. It does a nice job and it is free to use. To add a bit more info to the post above, 3DS files work fine, but if you have very large files then you may run into limitations here. This comes into play with very high surface counts such as custom stairs with complex geometry in things like spindles and railings. DAE can handle larger files than 3DS can handle. DAE also has possibilities for layers that 3DS does not. Still a work in progress though for both Chief's export routine and Blenders new layer standards when that arrives. This would make Blender an even more valuable asset to your tools set. They do have a plug in for Octane that works inside Blender, but I have not used that myself.
-
I quite agree with what Graham says. Where I do see the value in using a program such as Blender, or Blender in combination with a professional grade rendering engine such as Octane is if your focus is on producing animations. Even then you would need to evaluate whether a program such as Lumion would meet your needs, or if you really are serious enough to invest the time required to develop the needed skills. What I like about using Octane, is that even if I don't use it for animations, I can use it for a single high quality image which takes a matter of seconds with the right equipment. A good working knowledge of lighting and materials will still be required. Octane also has a few other features that I really like as well. Blender is a fabulous program, and in the right hands one could do almost anything with it graphics wise, but in reality I mostly use it to convert Chief files into the file format required for use in Octane Render. The good news is that you get to choose. Why not check a few things out and let us know what you find.
-
flat 2x12 laying on roof to accept rafters from reverse gable
RodCole replied to Snoodle's topic in General Q & A
Headed out the door right now. I will try to get back to you later on this evening. -
From my experience you will need another CAD program in order to organize your parts from CADwork into Chief as separate symbols. You may be able to do it from CADwork, but I don't know enough about CADwork to say. I use TurboCAD Pro Platinum for the conversions that I work with. I would think that one of their entry level programs might work just as well for your purposes since your design and machining processes are satisfactory as is in CADwork. The real challenge that I have found when importing separate objects that comprise one complex object is being able to properly align the symbols once imported into Chief. From my experience it is the bounding box that is the key to this task. Trying to work with numerous insertion points could work in theory, but in reality it is more trouble than it is worth. The basic idea is to place reference objects in Chief that will set the outer bounds of the bounding box. Lower Left, Upper Right, and make them very small so they do not show in presentations. I use 1"x1"x1" cubes for my conversions. Export these out of Chief and set a reference marker and record your elevation settings for future use on import. Don't know why, but I get much more accurate results when using the bounding reference exported from Chief. BTW make your bounding box reference large enough so that it will enclose any potential changes you may want to make in the future. Insert your component objects into a copy of this file and then import this file into Chief as a symbol. Use the symbols bounding box to move it into alignment with your reference point and then move it to the proper elevation. Do the same for all other object components with your choice of layer assignment for each object. Still experimenting with instancing and the Symbol's Replace Geometry option, but things look very promising. Hope that is helpful. Nice work BTW
-
Nothing wrong with the advice above regarding videos and other tutorials. It is just that I have found sometimes books such as Terry's can save you some time because they are designed to be both training material and a reference source. I will check out your web site as well.
-
Please provide a bit more background on the type of projects you are interested in using Chief for, and your particular field of interest. I would also recommend Terry Munson's books on Chief Architect. Check out his web site.
-
Use a box, in floor plan view. Orient it to be perpendicular to an exterior wall. Size it and tilt it up to match the pitch of the roof. Move it to the correct elevation in a cross section view. The tricky part is aligning it to the valley, but you can get it close in floor plan view. Once in place you can trim the ends using solid subtraction methods in floor plan view. Rafters are solids made from copies of rafters. Create what you need to cut the bottoms off in a cross section view. Sounds like a lot, but it can go fairly quickly once you get used to it and it is accurate for the most part.
-
Nice to see the effort to bring 3D details into Chief. Gene, it appears from the drawing that you posted that the 2D details done in Chief were created as separate drawings. Again, I appreciate the effort, but it kind of defeats the purpose of creating a 3D model only to have to draw the 2D details of the model. Not only should the 3D dimensions be available in the 2D vjiews, there should also be hidden lines as dashed as well. These types of details produced from solid models has been around quite a while. I suspect you already know that though, since it seems the objective is to arrive at this destination using chief. BTW, you can actually bring dimensions placed on a 3D UCS or Workplane into Chief now. They are no longer dimensions, but rather surfaces that can be displayed in 3D space in Chief. So far as I know this only works when importing a 3DS file though. Still, if you are going to go to the effort of bringing in the model, why not bring in the dimensions in 3D and simply pull the camera views in Chief? Been working with this off and on with Chief for a while now. What I am looking to achieve is to be able to bring in symbols that contain dimensions of such things as framing hardware where the dimensions are already in place. It would work now if Chief gave a bit more control over layer settings of the component parts of imported symbols. Next best is to bring the dimensions in as separate symbols. It does work, but maintaining proper alignment to the dimensioned objects when inserting the symbol is tedious. Curious, has anyone been working with the Replace Geometry feature of symbols? It has the potential to bring instanced objects into Chief to replace existing symbols that need to be updated to match current needs.
-
Yes, as a sub. Just though it might be a good opportunity to touch bases just in case circumstances change for either of us. But, I do understand what you are needing, and right now I am already working.
-
I am pretty busy now, but I work in Lake Oswego. Might not be a bad idea to keep in touch. IM if interested.
-
I find this issue as well, but it does not require that the Block be scaled for this to occur. Another odd issue with CAD Blocks containing text is that when several Blocks are group selected, the Blocks can become overwritten by other Blocks in the selected group. Seriously not cool. Been meaning to report this to tech support, but have not taken the time to do so yet.
-
Mark If I am following what you are trying to do regarding exporting both framing and wall surfaces into 3D PDF files. What I do is export each set of geometry to separate files and then do an Extract From to import the geometry into a composite file in TC Pro Platinum. Select each group as it is brought in and change the layers as req'd. I don't actually mix wall surfaces and framing in my models, but the principle should work though.
-
Yes, I do own a license to Octane Render. Where Octane shines is that it is an interactive and unbiased ray tracing engine that is GPU based. What that means is that a full on ray trace app that you can fly round in with very little delay before you have a good image, and only a few seconds longer for a finished product. What I find to be one of the best features is the ability to change materials on the fly. Octane is also becoming a very prominent player in the production of motion pictures due to the quality and speed of production, and also very reasonably priced for small shops for the production of animations and fly overs.
-
Don't overlook Octane Render. Very Progressive features. Not PDF though. You will have to convert to OBJ to use your models.
-
I do this quite often. What I have found though is that it is more about the interest of the client to want to use the model than the actual modeling itself as to whether it is a worthwhile endeavor. Right now I am actually doing more commercial steel framing than I used to and this has been quite a learning curve using Chief. What I am finding to be the real issue is not whether a particular program can allow you to visualize the 3D model. There are many good programs out there. What is more important to me is having the ability to model all of the components quickly and accurately.and then get that accurate model into a form that the end user actually would be willing to use.
-
Alternatively to Chief's ray tracing your new video card will run Octane Render fairly well. Check out the free trial version of 3.0 at Otoy's web site. CPU is not an issue, but you will need to convert the files to OBJ format.
-
Have you looked into Octane Render? Version 3.0 is available now for $399.00. You will need a good cuda enabled Nvidia video card and the time to learn how to run it, but my typical render times are in the 2 to 3 minute range. Of course, the more complex the model and lighting the longer it takes, but still fast compared to your current time. Like Graham said, if you post the plan folks can take a look at it for you to see if your time frame can be sped up using Chief. If I can find the time I will run it though Octane and see how that works out as well. Good luck
-
You can also approach this type of construction using Chief along with other more powerful 3D modeling programs. The basics are to create the model in Chief and then place custom symbols of the more complex 3D geometry.
-
I live and work in Lake O. Have you checked to see if there is a local users group in Portland already? Keep us informed if you don't mind.
-
Also keep in mind that the reflect tool can do things that one might not expect. I found recently when working with metal C channel floor framing that reflecting a floor section actually reversed the open or soft side of the C channel.