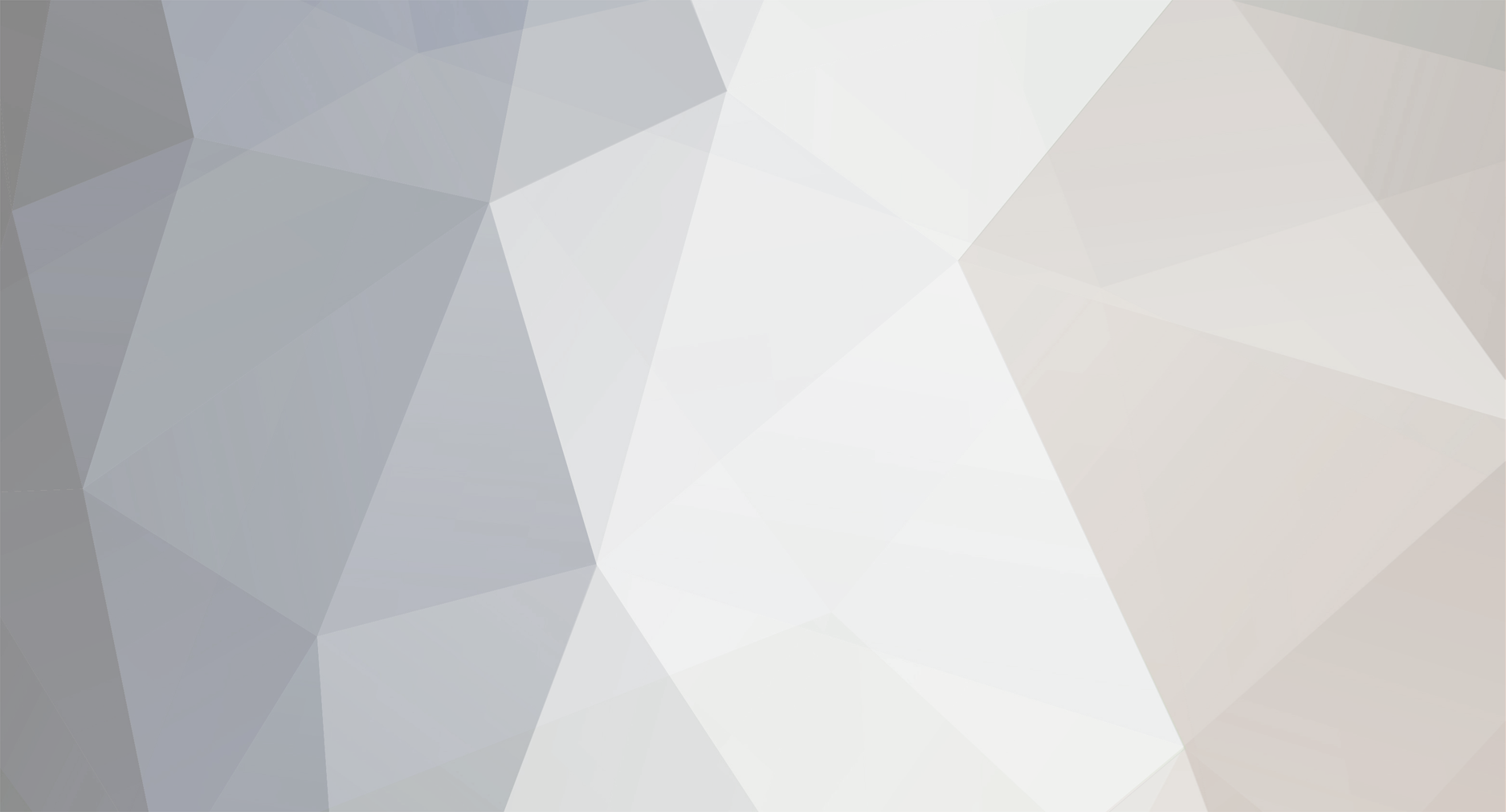
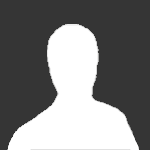
RodCole
Members-
Posts
626 -
Joined
-
Last visited
Content Type
Profiles
Forums
Gallery
Everything posted by RodCole
-
Hi Robert Sorry for already being a pain, but what I would suggest is to set up anno sets for use in your kitchen design work. That way you can work with the settings you want now and can grow into other aspects of Chief's as well later on. I know, I know, anno sets already, really. There are a lot of advantages though, you might also want to consider creating anno sets for each large scale plan and elevation view that you like to work with as well. Defaults, as you have found, are req'd learning, but to really make Chief work for you it is also important to learn about Layer Sets and Anno Sets as well. If you post your plan others will be better able to help you with specifics.
-
You create the layer definitions in the other app and assign the materials in Chief either on import or you can edit the material definitions any time later. You can create the trusses as either 3D surfaces or 3D solids in the other app and Chief will import either one just fine from my experience. I am starting to think that I may need to create some sort of readme file to go along with the U3D file so folks know how to use it. In general, being a U3D or full 3D file in the PDF format it can be viewed using adobe's free viewer that you would use to view ordinary text documents. The material definitions for the U3D file have to be set up differently than is req'd for display in other programs such as Chief. I am more focused on getting the content created and converted for on site use at this time. To use the U3D file check or uncheck the layers you want to either show or hide and then use the cursor by hovering it over the model and using the icons on the top to control the mode of camera movement. It also has the ability to section the model and many other capabilites as well. My personal preference for the render mode is shaded illustration found on the contol bar at the top under the blue cube with a small green rectangle. I also like the cubic lighting mode found under the lampstand icon. It seems to me that this type of design deliverable that uses a free viewer and does not require any previous CAD experience holds a lot of potential for construction applications. The problem seems to be all of the marketing hype that has led people to believe that they have to buy that expensive BIM program in order to use these technologies. Nothing could be further from the truth. There are quite a few work arounds, or hoops to jump through in order to create a file of this type, but so long as the content is created accurately the converion process, other than layer issues, is working fairly well for me now. Did you check out how Chief's trusses do not show correctly in 3D in the U3D file? Note: the Navigation icons do not display until the cursor is over the model area. Great app, but this part is not very intuitive to say the least.
-
Unless I am missing something, why don't you just model the truss in another app that will allow you to create an exact model of the trusses and bring it into Chief as a Symbol? I always put a note on the plans that the truss depictions are a graphical representation only, and that the truss drawings will be supplied by the truss manufacturer. Code requirement anyway. There is another thing about using a symbol rather than Chief's trusses and that is if you want to produce a U3D file Chief's trusses do not hide surfaces correctly where the outside source method does. This actually saves time in that any camera views you create for CDs are now correct. I still try to get by with Chief's trusses as much as I can, but if the need arrises I don't hesitate to create a symbol. Quite often I wish I had rather than deal with Chief's issues. The general process is to enter the coordinates of the joint connections and draw lines and offset lines so I can use a polyline to create each member. I have found that if you keep evey member on the same layer the member intersection will not display correctly in Chief. Just need to have a way to create unique material definitions and all is well. BTW check out the U3D file I posted in the "What Chief CAN" do thread Joey started in the Chatroom forum to see what I am refering to about Chief's trusses not displaying correctly in when exported.
-
I just posted this U3D file in another thread, but it seems at least somewhat related to what RL-inc is talking about regarding what can be seen on the screen, or more regarding a 2D screen. Play with the render modes and lighting to see what suits you. This model also has the components organized into layers by group. The basic model was done in Chief, but I did use other programs as req'd. 3D PDF file Export.PDF
-
IMSI used to have a competive upgrade program where if you already owned a qualifying CAD program you could buy their products at prices far lower than what is advertised. Last I checked Chief Architect did quialifyfor the competitive upgrade price. BTW you don't have to trade your old program in, you just get the new one from them at a reduced price. Don't know if they promote this, I think you have to know about it and ask their sales department for the discount.
-
The only thing I can say for certain is that Chief is always improving, and I am always learning new things. Don't really care about percentages myself. I am more interested in what I am able to accomplish and how long it takes. From that perspective I feel a better question might be, how much do you know about Chief's default settings and how well do you organize your workflow using custom templates. I think the answer to that question comes down to each persons unique needs. What I have found is that the more I learn and implement Chief's Defaults such as Layer Sets, Anno Sets, Framing Defaults, ect the more I want and the better and faster my work becomes. For my own interests it is more about where I am heading than where I am now. And that is actually where I see Chief's strength, in it's flexibiltiy. It can be set up to do any number of things. The hard part is that you then have to know enough to be able to set it up the way you want. Some programs box you in to a certain method of operation based on the available choices in their dbx. That has some advantages where it comes to certain industry standards. But, Chief can do those things as well, you just have to do it yourself.
-
Dennis Where do you plan on putting it?
-
As interesting as this looks, I am more interested in a similar offering called, I believe it was, Brigade. Odd name, but it is a real time ray trace gaming environment very similar to Octane Render. The difference is that Brigade is real time with no pixelation when the camera is moving. From what I understand the gaming visors can be disorienting or even cause nausea. Not so good for your average home design customer as it is for hard core gamers. The idea is great though and will hopefully become more useful as the cost come down and the technologies improve. From what I understand the next few months will see some major changes in this arena. There are beta versions of some of these new technologies available, but I have not taken the time to check them out.
-
Curious how you folks are dealing with window schdules for Auto Floating Dormer windows on the attic level? I prefer to have the window schedule on a per floor basis along with each plan level. But, the attic does not fit with that scheme if the scedules are by floor. I have been experimenting with a few methods lately and it would be nice to know how others are dealing with this situation. Thanks
-
I used to leave it on too. I do find times now when I do want to change the default for effect.
-
Rather than create separate layers for those items by floors, try the "Defaults-Camera-General-Options section at bottom of the page and check or uncheck Show Lower Floor Overview box". What I have found is that if you know the type of view you want to have then set this before generating the view. I used to only use this option on occasion, now I am finding more and more ways make some very interesting uses of it for displaying the type of views I want. Once you get familiar with this approach then you only need to create a few extra layer as req'd.
-
You are exactly right about not being able to extend Solids once they become shapes. The trick is to leave them a little long in the first place and then be very careful with where you chose to place your subtractions. I use a Solid Box the size of the valley plate stock and then rotate it upward to match the angle of the pitch of the roof. Rotating it to align with the valley boards is the tough part, no make parrallel tool available. BTW you can still extend the box after it is raised into position above the roof sheathing, just not after a subtraction has been performed on it. Hope that is helpful.
-
Mike What I intended to say was that I did in fact leave a space for the sheathing as would be expected. I just did not show it in the first pic. A latter response shows the sheathing in position as would be expected. Since the roof diaphram was not constructed as the engineer requested and the plans detailed. We then had to get together and figure out how to construct additional shear panels in order to meet the requirements of the design. Sorry about that, been working late a lot lately, probably not as clear as it could have been.
-
It really does not take that long to model 3D Solids in Chief, just be sure you cover your bases in 2D as well. Then you can decide when to use and when not to use 3D Solid modeling techniques. I do hear what Larry is saying though regard where one choses to invest their time. I for one do actually like the modeling process, and the finished product as well. The best solution I have found is to use other Solid modeling programs that are much better at this than Chief then import a symbol and even the 2D drawings if needed. Again, to each his own. Good luck.
-
The model I posted does have the valley plates above the roof sheathing. If a person wanted to go that far you could model the sheathing and even provide subtractions for cutaways or whatever. The problem I see with the modeling approach is not so much the time to model, it is the lack of fill available in 2D views. Chief's 3D Solids capabilities are very good, but the tools provided to work with them are way below what they should be for any serious attempt at modeling. BTW where 3D Solids modeling does shine is when you want to create a U3D file. 2D doesn't exist in that world. You even have to model text and dims depending on the programs you use. Funny thing is that Chief does the text and dims great when importing, it just does not have a way to create it's own 3D text or dims. Unless I miss my bet, the 3D computer world is about to take a major step forward with the new Windows 10 apps being developed. Edit: I recently had a project where the 2D plans where very clear that the roof sheathing was to continue under the overbuilt section in order to provide the required shear the engineer requested. I even spoke with the framer and explained why it needed to be done this way. He said something about how he already knew how to do this as I was leaving. Myself, the engineer, and the GC just finished working out the additional shear panels required to fix the issues his method created.
-
Here is a quick model of an overbuilt roof using Chief Solids. Here is a pic, and a very simple plan file. I actually had more trouble working without my default settings than doing the roof framing. Just thought a few folks might like to kick the tires. Edit: Just noticed that I did not meet the valley plates at the top. Long day. BTW the framing is on layer "Framing Roof Rafter Cal Overbuild" Cal Overbuild - Chief Solids.plan
-
I don't work with AC anymore, but I do work with another program that deals with PS in a similar manner. BTW you can print to PDF and convert the PDF to CAD. At least I can with the program that I use. A bit tedious as you have probably already found, and it will be at the scale of the drawing output. Scaling up is an option, but again, it is still 2D and one needs to be very precise when scaling in this manner or the final product will not be the correct size. Another way to deal with AC PS is to flatten an Orthographic view and output to scale. Last time I used AC the lines were tiny segments rather than full lines. BTW the trend in commercial is as you are describing regarding drawing sheet order. Not so important for residential though so far as I can tell.
-
I get it. I used to work on intel fabs for serveral years. Wonderful experience in many ways, but the bizzaro world in others.
-
Interesting situationn you are describing. What this reminds me of is the I Ching with it's hexagrams with one strong line at the top and all other lines yeilding. Also it's counterpart with one yeilding line at the top and all other lines being firm or unbroken. The stong line at the top is the power structure of the army. One commands and all others follow, which is also the model of our modern day Project management scheme that has it's roots in the later parts of WWII. The topmost yeiding line represent creativity or beauty while capturing the talent of a variety of skilled craftsmen. Sounds like you are tasked with dealing with both strong minded creative individuals as well as having to conform to a rather rigid overarching management scheme or power structure. Like I said, interesting. One thing I seem to be running into more often now that my ray traces are getting much more realistic and real time is that customers are becoming much more involved in the design process than they ever were before. For the most part I like it, but there are times when it gets more difficult to navigate when customers choices and egos get involved. So far so good though, at least as far as the customers getting what they want is concerned, and that is very important to me.
-
I had a situation recently where I felt that a particular design altenative was much better than the one the owner had chosen. I simply told her my honest opinion, and that once the project was completed then everyone is a critic. She thanked me for being honest, and for respecting her right as an owner to choose for herself. There are a lot of reasons why I still like my idea better, but that, as they say, is history. Years ago I framed a house for some folks that had been living in a trailer for a period of time before they built their new home. Because of their experience of having lived in the trailer with walls so thin that there was next to no sound deadening they decided to insulate each and every interior wall in their new home. The home was on a concrete slab since the owner was a retired concrete contractor and did that phase of the project himself. The part of this story that applies here is that when the mechanical contractor showed up to run the overhead ducting he ran a single duct that opened both into the guest bath next to the toilet, and straight through into the greatroom. Needless to say that when the toilet was flushed it was rather loud and could be heard thoughtout the house. Edit: BTW the general contractor, who also prepared the plans for these folks had been known to work up his designs on the back of envelopes. Back in the day you could get by with that a lot more than you can today.
-
Joe Highlight the Layout Box and then select the Layout Box Layers icon from the Edit toolbar. Select the Layer Set from the dbx. For plan views you can also select the Layout Box and open it and then choose the Plan View tab and choose the anno set. Anno Sets for other views are associated with the Plan and handel Layer Sets as you already mentioned. I actually like using the Layout as kind of a Dashboard to navigate to many of the setting I use on a regular basis. I have the Project Browser docked to the left of the screen with the Pages section open. I also use a hotkey for quick access so I only use it when I need it. I still find that there are times when I just want to change settings without going through the Layout though. We have seen threads before regarding whether Layer Sets or Anno Sets are King. That doesn't really mean anything to me. Seems like personal preference to me, with the exception that I would certainly not leave Layout Views off ot the list of options.
-
Joe The folks at StruCalc use Chief themselves, or at least they used to the last time I spoke with them. You might try giving them a call to see if there is a posibility of having some type of interoperability between Chief and StruCalc. Too bad we already know the answer on Chief's end regarding plug-ins. Hopefully that will change. Woodworks has a plug-in that used to provide a limited form of interoperability between it and Revit. I have not upgraded to that program ever since they went down that road. The problem was that the interoperablity did not extend to the entire program, just one module, and it only worked for studs in Revit at the time. BTW the price of the program went way way up, imagine that from the leader of free and open interoperabilty. If I am following your statements regarding wind loads that is basically it. Why it is getting to be more important to me is now that the construction industry is getting a bit busier it is even more important to have the design as close as possible in order to streamline the design process. During the bubble we saw turnaround time with engineers go from a couple of weeks to a month or more. Hope we do not see that again, but I just want to make sure everything is as close to a go as I can before sending it out. Another thing that comes into play at times is the floor diaphram and or the retaining wall and the anchorage to it.
-
Yes, Bending and Shear are very important, but the programs themsleves can potentially give you a passing grade when the member may not actually perform well at all given the design conditions and loading. So far, in our area wind is generally the controling factor, but Seismic is important as well. Yes, there were no labels available at that time, and even worse the macros would not work in a cross section elevation view. I could get some things to work by doing a CAD Detail from View and then placing that on the floor plan, but it just got to be more than I wanted to deal with and on top of that it was a very tedious process. Anything I can help you with don't hesitate to ask.
-
The main criteria that I use is deflection. Not just code L over whatever, but the actual deflection measured at points along the structural member under the design load. Some programs will allow you to just move the mouse along the graph to check deflection anywhere on the member. How a member actually performs in a meaningful way in a structure is more related to what can be seen external to the member such as how far it will sag or creep, not the forces that are internal to the member itself. This approach generally produces a very conservative design, but there are generally no problems down the road with a professional engineers calculations. Depth is the first thing that makes a meaningful difference in performance. Second would be either the member spacing or the lumber grade / type of engineered member, kind of have to play with these two in order to decide the best approach. Third, and that is a very distant third would be width, but sometimes you just are not given any other options than to increase the width no mater how poor a solution that may be. I take it you are working on a macro to these purposes? What I would like to see is a macro for calculating wind loads based on area. Gave that a try a few versions back and to be honest just got completely frustrated with the whole process. Hope everything works out well for you.
-
If you really want to know what are considered to be industry standards for line weights for computer generated plans using advanced modeling programs then you might check out some of the publications on Revit. Seems like I remember that being covered in one of my books on Revit Structures a few versions back. That being said, the information being posted here is as valid as any in my book. IMO the folks that have been using a 3D architectural modeling program such as Chief over a period of time have the experience to know what works for them in rather complex printing situaltions. My moto is "I buy experience all day long".