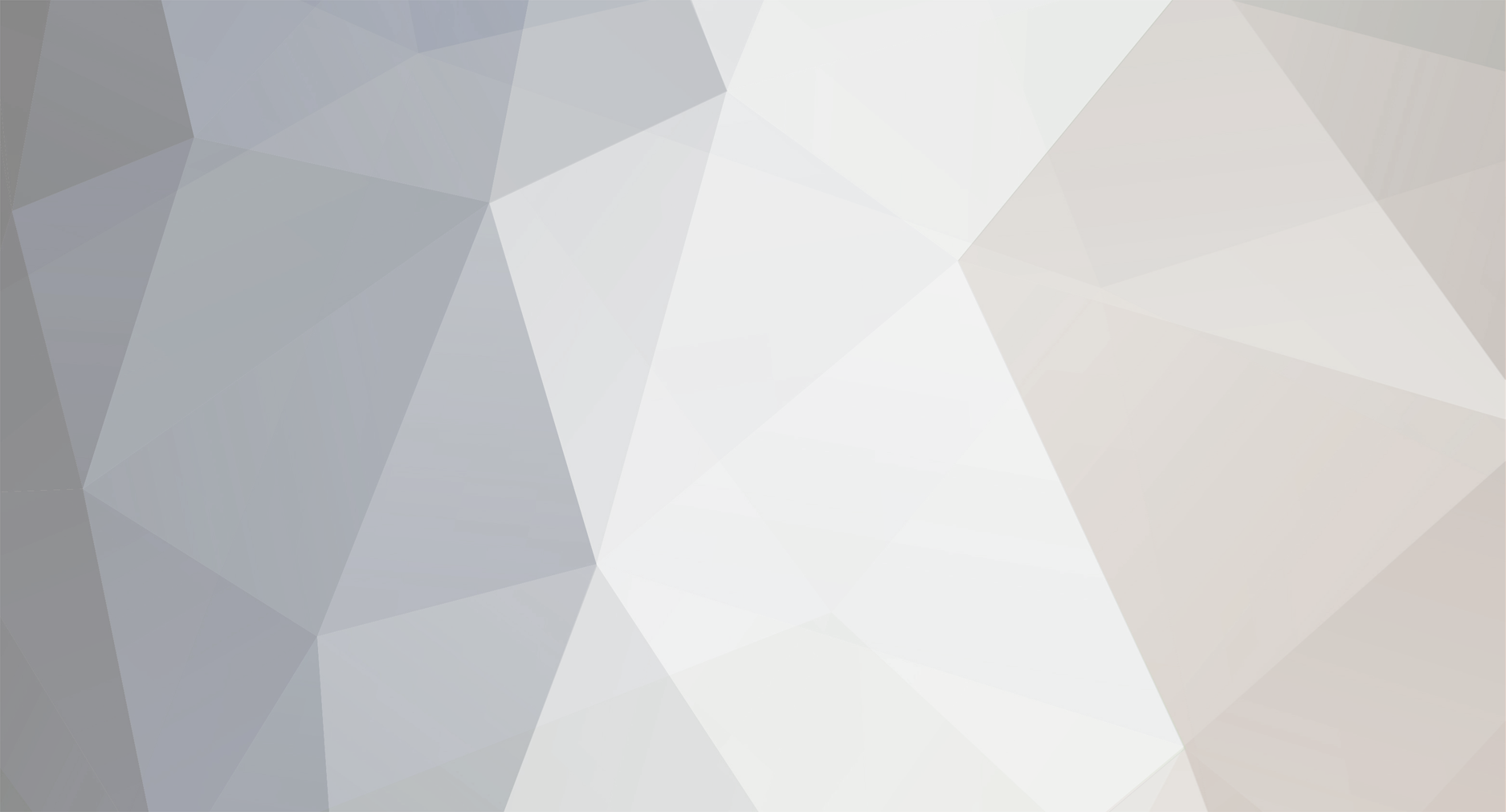
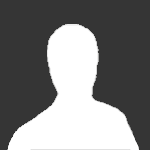
ValleyGuy
Members-
Posts
321 -
Joined
-
Last visited
Content Type
Profiles
Forums
Gallery
Everything posted by ValleyGuy
-
You have the right idea, just use a copied layerset in the one plan. I've messed around with it a little bit. It isn't bullet proof, but it gets the idea across with two looks in the same plan (I haven't pushed my luck with three views...). Make a copy of a layerset with additional copied lines for the windows and doors, corner boards, and roof (copy each existing line so they will show up in your different camera views). Copy and paste in same position an item that you want to change, then immediately change the defaults and layer of the duplicate item. Simply keep track what you want showing on each layerset. To change the siding, I used wall material region with the same thickness of siding and put it to the appropriate layerset. When you use an existing saved plan view or take a camera view, you have the live active features and just need to choose your layerset to switch back and forth. There are some draw backs like soffit showing on one but not the other, some windows aren't exactly all black. Needing to turn off the gutters and ridge caps as they will conflict each other is something you'll just have to play around with to clean it up (at all costs, try and not duplicate the roof as it is the biggest pain). Use 3D solids (...good for missing soffits) as work arounds. It is always a better practice to either finalize the structure or finalize the colour scheme so you don't end up having components that are duplicated getting out of sync if you decide to make structural changes. I would encourage the colour selection to be early on so you can then eliminate the duplicate that isn't needed and minimize computer chaos and excess time chasing all the loose ends. If this is a little too much maintenance and fooling around, I have also made a customer specific folder with the exact siding, window colour, corner colour, soffit, fascia, roof material. Use the appropriate paint / material roller to quickly change the house features. This has been less work and a lot less risky in not removing a duplicate or replacing something turned off when doing x-sections afterwards. Everyone that needed this made a decision almost immediately upon seeing it so sometimes spending too much time isn't worth it. Hope this helps, Shayne
-
It is nice, have you experienced any issues with the controller seizing up in 3D as I have explained above?
-
@mthd97 I'm tagging you here as you were asking in another thread how the Space Mouse Enterprise worked in CA with a Mac. I've had it for about a month and here are some things that may be of interest to you and anyone else thinking of getting one. In short, if any of you haven't got one, GET ONE, it is a game changer for sure! Some notable differences specific to Mac: - CA doesn't (according to 3D Connexion) fully support the Enterprise model which creates a couple of setbacks. The most notable - when trying to navigate in 3D while holding a tool or selecting something will glitch the mouse and the joystick will eventually seize (all the buttons will still work flawlessly). Example: select a door then try moving before deselecting it will cause problems. If you deselect before moving, the joystick works fine. Shutting down CA and reloading is all it takes to get back to using the joystick again. Quick to do with a Mac, but still a pain. This only seems to happen in 3D views while trying to move with items / tools that are open or in use. 2D plan view and elevations don't seem to have any problems. *** If anyone has a fix for this 3D view problem that I am experiencing, I'd sure appreciate any help you can offer.*** - the only other issue that I see in CA is there are 5 buttons that do not seem to want to respond, the elevation buttons (R/L, F/B, Top/Bottom, Fit) and Menu (menu is for the Spacemouse menu and I'm sure it probably gets reprogrammed to something more useful). I initially thought that these were going to be a huge loss, but now that I'm getting more comfortable with it, I'm not sure that it matters to me. Here are the best features in my opinion... - Tools galore at your finger tips. I'm glad that I went a step up from the PRO model as the Enterprise has many more buttons to use. Not only does it have many more programable buttons for tools, but is also has the additional Enter, Delete, Tab, Alt, and Spacebar keys, all of which are real time savers once you get the muscle memory working. I currently have about 125 tools loaded and the rotary dials are basically endless - meaning any of the 22 last working options can just keep on bringing up more and more rotary dials of tools. And if you are wondering.... sorry, no library items - only tools can be linked as far as I am aware. Well, not any library items that are not defaults for a tool. This is because it works off of macros (hot keys). Example, if you just wanted to pick a chair out of the library, it couldn't be on a rotary dial option because CA doesn't have a hot key (place object tool) for random chairs. The many keys of the Enterprise also may minimize the multiple coding issues I've read about with the PRO model, as it appears to only have 4 buttons to accommodate all the tools. The Enterprise is corded via a USB port, so if cordless is a must, it may not be for you. I personally don't find the cord an issue in my office or on the clients kitchen table. - Hot Keys: remembering and having the required finger dexterity are now eliminated. A bonus benefit is I basically streamlined all of my hot keys. No more Control, Shift, Option, Command + letter/number. W1 through W9 for walls, D1-D9 for doors, C1-C9 for cabinet items, F1-F9 for framing, etc, as I no longer need to remember hotkeys. (I do still have a few that I just decided to leave as is.) I couldn't remember 125 hotkeys anyways, and now I just have to remember 22 keys to access the 125 tools. This also saves endless miles and time on my other mouse travelling around to different tool bars. In addition, I was able to program a two-step process with ease. The centre between two points is a secondary tool that only appears after an item is commanded to be centred (no direct hot key ability). Both commands have now turned into one choice on the rotary dial. - Tool bars: I have basically eliminated all of the basic toolbars. I now have space for custom toolbars full of library items. This saves an enormous amount of time not having to drill down through the layers for common library items. - Mac only gets a 4 unit rotary dial option, without picture icon ability. I would have liked the 8 unit dial (PC Computer option) to save a few more selection mouse clicks, however, having words instead of icons allows better flexibility especially if icons aren't available (any of the Defaults), and also allows for multiple words vs a single icon. Sometimes a few words helps to remember the tool, especially if the tool isn't used too often and the icon isn't remembered easily. The really nice part is that the rotary dial is always right where your curser is, so the choice is only a small movement with a click and you are right back working again. - And now the controller: the smooth movements with great control in 3D walk throughs is really a treat for me as well as my clients. It brings the control movements to a whole other level. This also makes the working end of business more efficient and enjoyable as well. It is so nice to have zoom and pan in plan view with the super smooth joystick control. It makes zooming in to place dimension tools accurately with the ability to travel 75' away, zoom in quickly again and place the other end without clicking anything else or having to take additional steps like temporarily suspending the dimension tool to activate the PAN tool, or spinning the wheel on my other mouse. I don't play video games, but my kid said it's like a dad's version of a game controller. I am not sure exactly how much more efficient the Enterprise will make my workflow go, but I am convinced that it will be the gift that keeps on giving the more comfortable I become with it. I'm sure that the cost of it will be recouped very quickly and the enjoyment of using it will be long lasting.
-
We are able to make any type of rail(s) that we need, just make a mldg and place it in your library. Replace the default rail(s) and rotate, raise/lower until it is what you want.
-
Solver (Eric) made a two or three part garage door video that you may be able to still find on his youtube channel that is very informative and should meet your needs.
-
How to Add More 3D Objects in Electrical Child Button
ValleyGuy replied to DHerb2014's topic in General Q & A
-
I believe the key is the direction of wall travel. Clockwise in my plans produce proper interior / exterior materials. If I draw one wall counter clockwise, it will reverse the interior / exterior materials all while showing proper in plan view. This is w/ or w/o the 'Auto Reverse' checked in the defaults. I'm putting an addition onto an as-built right now, and when I have two walls drawn (clockwise) and start the last wall coming out from the existing building instead of continuing on - CA will make the intersection nicely in plan view, however it also consistently reverses the materials (the siding is the interior material and DW is on the exterior) on that last wall only, regardless if the wall position is clockwise of the last two walls. I run into the reversing materials quite often when drawing dormers, I just need to remember to draw clockwise and there doesn't seem to be any problems.
-
Unable to running dimension in specific SPV
ValleyGuy replied to GrizzlyBear's topic in General Q & A
You are correct, the best thing is to go through each one. Before you just copy SPV, defaults, layer set lines..., try and find out all the things that you are affecting, you will find that sometimes it is best to create from a 'New' standpoint. Layer set lines are a good example, if you happen to copy a line that has display checked for every other layer set you've created and you only want this new line to display on the current layer set, you will need to revise all the other layer sets. Keep plugging away, things get easier with each new little victory. -
Unable to running dimension in specific SPV
ValleyGuy replied to GrizzlyBear's topic in General Q & A
-
Hey Rene, ... the two extra walls in your toolbar, are they actual tools or are they just library items?
-
I'm fairly new at Chief so the pains of learning are still fresh - I feel your frustration as the learning curve is steep. This may also help support the information that you just learned above. It isn't really well explained in videos and hard to get a handle on just reading the help topics.
-
CA gives us the ability to control all kinds of things; line weights, text size, items dimensioned, colours, arrows. You can also turn on and off different dimensions for different saved plan views by saving a specific layer set to have a specific default set (that sentence could be a little overwhelming). For example, if you had a saved plan view for foundation - create a saved layer set, and a saved default set for the things you want to see and what / how you want to measure specifically for the foundation. Once you choose the saved plan view for foundation, you will have all those saved defaults at one click. You can do the same for the deck posts, or just use a different dimension layer set line with different defaults (units of measure, arrow, items to measure, colour,...) with in the foundation plan view. I put room inside measurements in orange on the main level to show the customer wall to wall measurements, and turn off the layer set when it goes to layout as the contractors don't want that measurement. On my foundation saved plan view, I use foundation dimension orange to show measurements for the sono tubes exclusively. (This works well as our building officials do not complain about colour on the plans.) It looks like you maybe are just missing the specific layer set, but you may also just need to add in a specific line to an existing layer set for the specific dimension you are seeking.
-
You may also be getting long linear lengths if you haven't checked the box for the max plate length found in the wall layers specification. Here is an idea that I use for the 'other' common board purchasing lengths. Contractors around here usually only order pre-cut studs (by the lift) for all the wall vertical framing, and 10', 12', 16' for plate material. I utilized the 'comment' part of the material list to add the trimmer studs to the pre-cut stud count (as you can't buy this exact length either) so the contractor doesn't need to optimize the oddball length pieces out of 10', 12', 16' lumber. I created a new Buy List, removed the lumber that I did not want to purchase, added in the common lengths (pre-cut studs) and those that will be created from openings (ie Trimmer studs), then arranged the selection order hierarchy. You will need to edit each line of lumber that you can't purchase at the lumber yard (ie trimmer stud lengths) to add in your comment (ie 92 5/8" pre-cut ). When you print off the material list, Chief will give a qty count of the different lengths of studs (trimmers and cripples) and select according to your hierarchy lines of the created buy list. Thus you get a nice neat list of oddball lumber sizes that have a comment to include them with lumber that can actually be purchased - the lift of pre-cuts. I believe that it gives a better real life count as most of the trimmer stud waste gets used for stuff that we don't usually take the time to draw (endless blocking, temp jigs, firewood...). If you just let Chief divide the linear add ups, I'm sure that someone will give you an earful when he has 5 pcs @10' plus 5 pcs @12' and needs 15 pieces at 92 5/8" = more wasted dollars cutting the long stuff and he'll need to scrounge some bad culled lumber to finish up. There may be an easier way, but this works pretty well for me...
-
I'll try and remember to do a follow up. Every review seems to have the same conclusions; once it's set up and the user gets comfortable with it, '...how did I ever survive without it...' seems to be the end result. As far as CA, I bought the Enterprise model with the hopes of significant work flow improvement because of the additional buttons on the unit. The enter button being controlled by the left hand alone should save a tremendous amount of effort as I currently only have a 7 button mouse and the keyboard. Here are some key things I'm hoping to gain from it in CA: -Having 96 "Hot Keys" at your finger tips without having to look at the keyboard will be an efficiency improvement. -Having to remember the sequence of acronyms, confusion of whether it was shift + letter or was it control + letter, as well as dealing with the errant finger dexterity mistakes should eliminated. -12 single buttons to pop up 96 tools / library items - I can see about 200 key strokes that won't be required to accomplish the same task. -The visual icon button on the screen should free up a little head space - remember the visual picture and not have to remember the hot keys associated with the picture. -There should be considerable fewer miles put on my current mouse racing across the screen. -Maybe even the multiple Macro ability could help with secondary mouse clicks, not sure about this option yet. -I'm hoping that the 'view keys' will make quick work with the elevations while in 3D. Pushing a button and having RH,LH, Front and Rear, Top and Bottom elevations may be very beneficial - especially with CA's recent teaser of available Dimensions in 3D views coming out in X16. This may minimize a lot of Cross Section Elevation tabs being open at the same time as all the views may be accessible from one 3D perspective overview - no more adjusting and measuring in 2D then having to jump into 3D to see how it looks, then maybe to plan view to adjust placement, then back to 3D...... - In addition to the above versatility within one 3D screen, I'm hoping that the 'Special View Keys' will act like temporary saved camera views. There could be the possibility to have three additional saved camera positions to jump back and forth from just by pushing a button. -And then there is the 3D picture navigation. I'm looking forward to having much smoother movements with greater control via the 'joystick' type control. Any zooming done not via the jumpy roller of my current mouse, will be welcomed for sure. How about all you Space Mouse Enterprise Users out there? Are you experiencing results like this or am I being optimistic?
-
You started me down the right path, Thank you. Incase anyone else needs to venture down this road.... Applications CA X15 -RH click, choose [Show Package Contents] Mac OS Resources Buttons Mine appear to have white backgrounds in the file thumbnails, but have a darker gray/brown background in preview mode. Just have to wait and see what comes out when the mouse arrives and they get inputted. Thanks again TeaTime
-
After searching old threads I believe that I am looking for a 'Resource' file. I can not seem to locate the 'resources' file on my Mac - maybe this isn't even the file I need to locate?? Where would I access Tool Icon Buttons? I have a new Space Mouse coming in a few days and would like to load the tool icon buttons from Chief X15. I found information and videos for PC's which appear to be straight forward, I just can't seem to find the file to get started. Like this, only on a Mac. Any help would be greatly appreciated.
-
If you mean that those two options are not highlighted for you to be able to use them, you possibly don't have the "Build Roof Planes" box checked off. Under the Build Roof Tool, or double click the Roof Plane Tool, either way will open the Build Roof Tool as the roof plane tool's direction comes from the Build Roof Tool. There really is no need to retain anything if you aren't auto building it, that is maybe why you can't select them.
-
Maybe give these guys in Toronto a look... https://artemis-studio.com/
-
If they are only decorative dormers placed on top of the roof... maybe someone has already done the heavy lifting for you. I found these prefabricated ones on the internet.
-
Hey Doug, I have seen some pretty intricate stuff like this done in foam covered with stucco. It is applied right over regular square stick built framing. Just the roof overhangs and fascia boards need to be worked out. Saves the weight and looks great. Where I'm at, we have a TrueFoam plant that will make pretty much anything you can design for their CNC cutout machine.
-
Good to know, thanks
-
You could also make your wall type material "opening (no material)" as the floor joist area is as Ryan says - filled with your wall layer materials.
-
I just did this a month or two ago. I used CA15 to take all the video clips in such a way to capture many different stages from a full vegetation lot through digging the hole, foundation, 1st floor framing, 2nd floor framing, roof with windows and doors and house wrap, finished house and patios on rough grading and ended with the landscaped lot and hard surfaced driveway. I made an MP4 video clip by splicing all the CA video clips together on my Mac's iMovie. No fancy editing as I have no idea how to do that stuff. All the work came from overlapping walk through paths in the same direction. The video is 93Mb so I can't load it here but I attached still shots from the 37 second video. The guys above are correct, it was about a day and a half worth of work to set up my library items (mostly chosen vegetation items with proper layer set specifications organized into different library folders), create additional layer sets for all the different plans needed, work out the logistics for the over lapping camera views, plus make all the additional items not already in the original plan. Four plans, 11 walk through clips, 10 additional layer sets, quite a few new items in my library along with manipulation of a few things like wall materials (to show the house wrap) is what was needed. I also made a two page set of directions so I can repeat this process in an hour or two now. I would say that the amount of effort was worth it as it is pretty cool and the customer loved watching his house come to life. If you are interested, I can email you the video to see if it is something you want to pursue.
-
I use the DWG for the survey certificate as well, it works fabulously with a little CAD outline of the building strategically placed on top. I import the PDF to my desk top then screen shot it (DWG), file it with the project, and then delete the desktop PDF. I put the DWG on a CAD sheet, fix up any additional markings and send it to the layout.
-
Thanks guys, that was it.