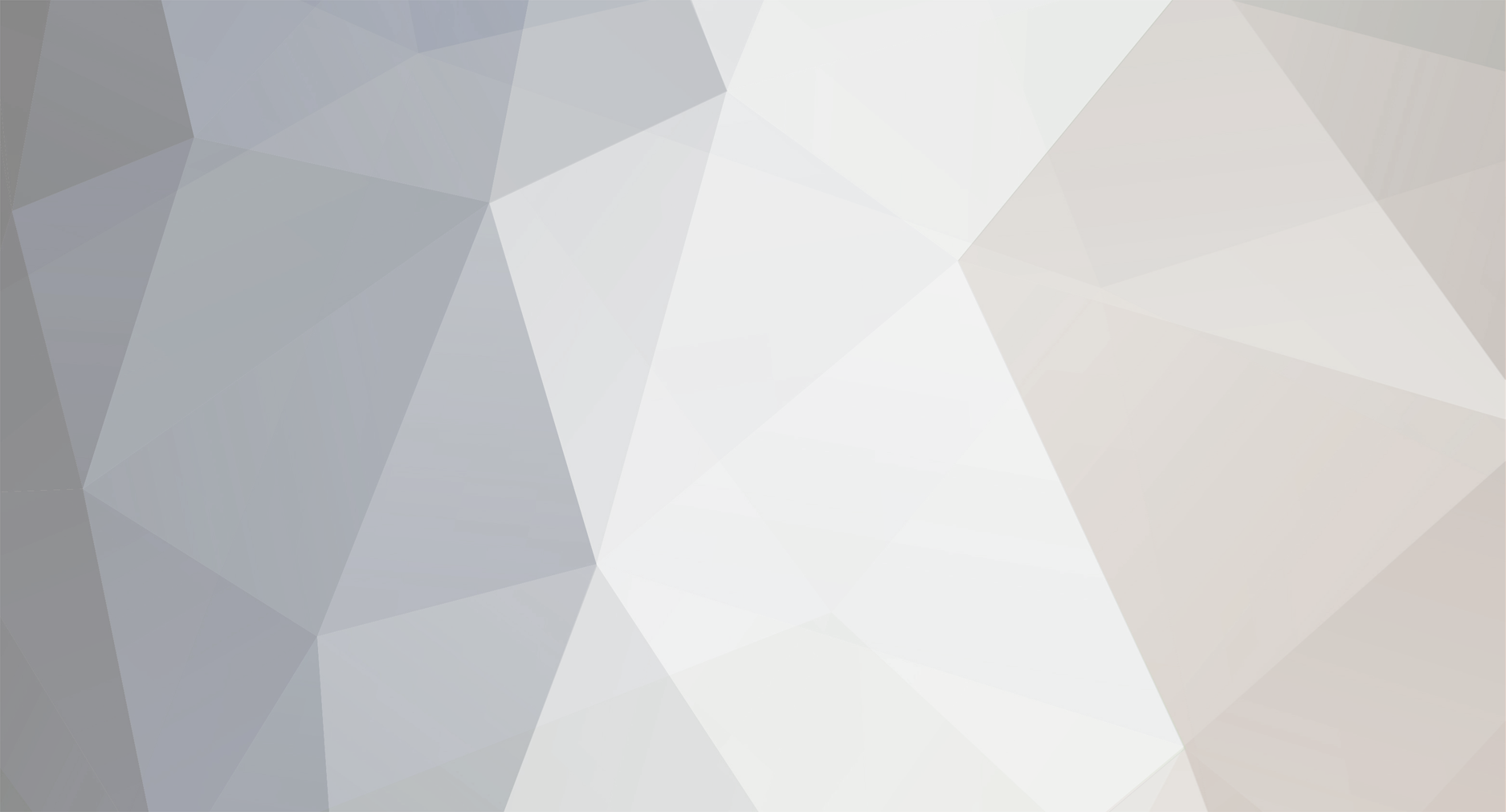
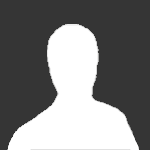
SHCanada2
-
Posts
1081 -
Joined
-
Last visited
Content Type
Profiles
Forums
Gallery
Posts posted by SHCanada2
-
-
1 minute ago, robdyck said:
In the example I posted, the exterior wall doesn't reference a cladding type. This simplifies my labelling process and and keeps me from needing to identifying walls based on cladding. I can save exterior finish callouts / notes for exterior elevations.
once you get to a tall wall, arent you going to need the RSI of the cladding to make the requirement? or do you put in R24?
-
2 minutes ago, robdyck said:
And computing all the areas is a pain,
yeah thats why I dont do it for whole houses.
-
...well it is still a work in progress...trying to see how much could be automated. I tend to do tradeoff because you can easily add insulation to the attic, and R22 /24 is considerably more money than R20. R24 is like double the price. That being said I also rarely do full houses to the level of calculating the efficiency. And computing all the areas is a pain, so I decided to put some effort into seeing how much can be moved to CA for the prescriptive method,..and if it could be done easily, and hopefully automated somewhat. Plus I see a lot of other plans, and I wanted to take the best of what I saw. Some of the larger builders just put down every wall/floor ceiling type in a table, and then they mark the section with callouts. I saw one that was like yours and then there was another table attached with the cladding type, and 3 resulting total RSI numbers.
Some background, my details are for the most part controlled by global variables, so I have a variable called DET-CLADDING that I set and then all of the details change the text to whatever that is set to, Stucco, vinyl, etc. That part works fine. But the question is how to get the details to convert to the RSI calculation automatically. As such I wanted something that was dynamic, which is why I chose the note schedule.
So what I did so far was to put what you see into 2(unfortuantely had to be 2 because it could not format) variables, DET-W1.1-26-Stucco and DET-W1.1_RSI. And then the note callout has those two in two different fields, and then I created the schedule, I was going to try and copy the Canadian Wood Council naming convention for wall assemblies, but it gets fairly extensive.
Anywho, my end goal was to try and create one global variable for each of the assemblies which auto generates the wall RSI, based on the original detail. so instead of DET-W1.1-26-Stucco, it would be just DET-W1-WALL(TYP) and DET-W1-WALL(TYP)-RSI , which is what the note is named. And then my plan was inside the DET-W1-WALL(TYP) macro do a $x="EXTERIOR AIR FILM"+"\n"+DET-CLADDING +"\n"...
and then do the same for the RSI. Which is why if I could format it properly, it would be better to just have one variable. ..although the RSI would probably be some sort of lookup..havent sorted that out yet
so if I got it all working, for a new plan, I would set the detail variables, and then put a note callout on the wall section, and do nothing else. the schedule would just shows the ones on the plan. Plus floors like those over garages would have to be done manully anyway
Are yours predetermined text boxes grouped as a CAD object and then you just have all of them on a single layout sheet? or how are you managing the changing stud spacing, insulation, and cladding?
I also thought about getting it out of the wall type itself, but that doesnt help with ceiling and floor. I suppose if the callout could get the room info, it might be possible, but i dont think that can be achieved from a macro in cross section.
-
-
actually that only works if there are numbers in the text, which I do not want. back to any ideas?
-
-
I'm endeavoring to move off spreadsheets, but I cannot get the formatting to work in the schedule.
I am trying to return multiline in one row.
I tried using tabs in a macro to try and align two columns within one column. That didnt work, see below
I tried to different columns, but the numbers dont seem to line up
I suppose I could use a uniform character font and type out the spaces, but do not really want to do that. any other ideas?
-
I use one pitch cad block on the front elevation, if all pitches are the same andvthats it. The roof plan view is quite nice with its pitches and artows, it's also where I dimension the eave. I don't dimension eaves on elevations.
Biggest problem is people ask for the pitch triangle. But I did see a plan the other day with the label in the roof like CA does it. Must have been CA...
-
that was an impressive find. ironically I have 3 concrete materials in my plan too
-
-
-
i use OOTB blue for the template lines and text.
It looks fine from my laser printer
-
I havent seen it, but I assume you could put a beam down the middle at ceiling level, put mono trusses on either side. ..if you do not want a vault
-
..beam and parrallel chord truss. cut the truss length by half
-
it happens to all the rooms at once, they just vanish, and then you have to go room by room turning them back on
-
1
-
-
i don't remember ...
-
yes, this was not a picture taken by me, it took me a while to find a clear example like this, on the internet. It seemed for most, the post either went all the way up through the railing, or part way up the stone went to the post, or most were not a flush beam
-
i thought you were going to say that
Most plans here are in ft-in, except for site plans, which are in m, and geodetic if required..in m. all the usual 12", 16", 24" for spacing are still used
believe it or not, there is a Canadian version of the simpson catalog, just becuase we are special
-
if it is solid beyond the flush beam, how would the water drain if it is 1x6 deck boards and the blocking+ beam is > 5.5"? just put on joist saver or bitumen based sheet and let the water run along the top of the blocking/flush beam to the end?
-
thanks, fur out the beam would seem to be good answer. ...perhaps make it like a torsion box
here they allow sonotubes for decks only,
-
does anyone know how these are structurally done with flush beams?
something like
where lets say the brick is 14"x14" on the outside
suppose the flush beam at the end of the deck is 3 ply. This would be 4.5 inch. and suppose the post inside the stone was 6x6. if the post was centered under the beam, the post would be 0.5" proud of the outside of the deck. Add to that the stone at a thickness of 1" or so, and it is 1.5" proud.
so are people just adding another cosmetic ply at the end to make up for this. If so, then the post itself would need to be box framed out with 2x4s, such that on the inside below the deck, it would come out around 7"? are the 2x4s just affixed to the post and thats good to hold the stone?
The above shows it on concrete pads, which I guess could hold it if it was deep like a footing, but for a standard 10 or 12" pile up North here, does this 2x4 build out sit on the 2" left on the pile beyond the post surface area. i.e. if the post is centered on the pile, there is not a lot left to support 7" of a boxed 2x4, especially given the post would be centered
and if the customer wanted 20" outside dims...just keep building out a 2x4 box and hope it holds?
thanks
-
I have this firepace setup as its own little room with 60" room hieght. The wall that delineates it is a pony wall with room divider on the bottom and normal stuccp 6 wall on top.
but outside is showing studs or something:
inside walls are no room definition
framing seems to look ok, more or less:
is there a better way toi do this?
-
4 hours ago, glennw said:
Make sure both objects have the same properties - weight, color, linestyle, layer.
that is the key, solver's video demostrates it.
thank you both
-
I still must be mising something. attached video is what I am trying . clicking S on arc, clicking on polyline. clikcing start of arc, clicking on polyline. no luck
Schedule formatting
in General Q & A
Posted
good advice