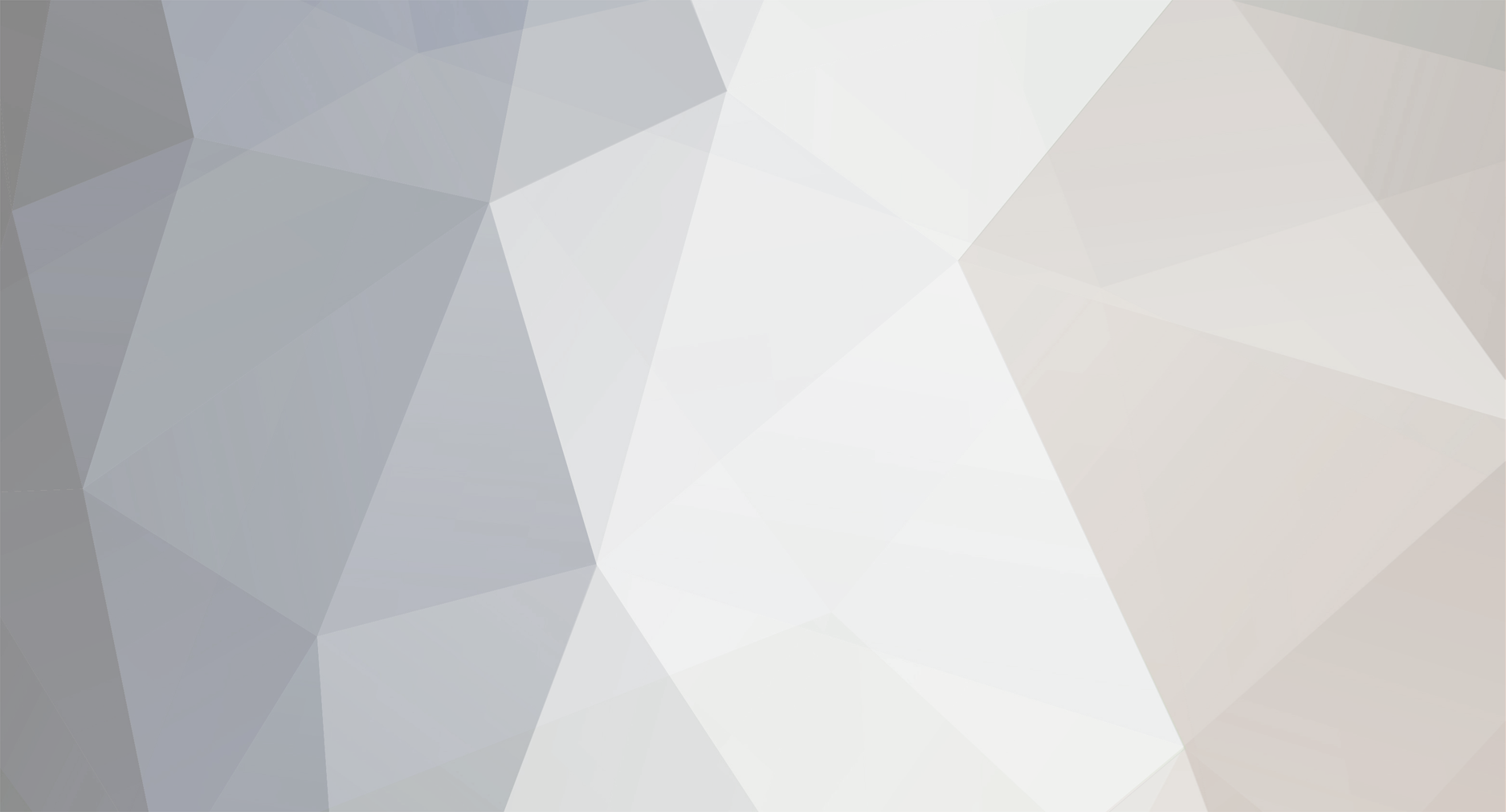
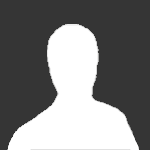
ValleyGuy
Members-
Posts
325 -
Joined
-
Last visited
Reputation
114 ExcellentProfile Information
-
Gender
Male
-
Location
Nova Scotia, Canada
Recent Profile Visitors
2989 profile views
-
Does anyone know how to reverse a 3D picture in a schedule?
ValleyGuy replied to ValleyGuy's topic in General Q & A
ooops ! Sorry @JKEdmo, I was trying to quote you and accidentally hit the solution button instead. ... still looking for a solution. -
Does anyone know how to reverse a 3D picture in a schedule?
ValleyGuy replied to ValleyGuy's topic in General Q & A
They aren't actually walls. They are 3D solids with texture at 12" thick. I used %volume% in the custom object field to give me the measurement, then told the schedule number formatting to use ft2. Length (ft) x Width (ft) x 1 ft will be the same measurement; volume or area. -
Does anyone know how to reverse a 3D picture in a schedule?
ValleyGuy replied to ValleyGuy's topic in General Q & A
Thanks Jim, this is a custom schedule and yes there is the interior and exterior options as well as just elevation in X16. Int & ext work for the windows and doors only it seems. The 3D elevation option shows a 2D straight on view of all objects. I really like the angled 3D look. -
Help Sizing Mulled Window Unit to Match Frame Size
ValleyGuy replied to DefinedDesign's topic in General Q & A
Lisa, it appears that you are trying to reinvent the wheel. I wouldn't spend the time to try and mess with the windows to make the exact framing. Carpenters have been using the window manufacture's supplied information to cut appropriate sized lumber for RSO's since the beginning of time. If the exact window information had to be in the plans, and I had the window manufacture's information that you are showing in the lower picture, I would put it onto a CAD sheet and mask off the info (headers, pricing, ...) that I didn't want to show and send that compiled CAD page to the layout. You have all the exact information, including your W-04 call out, already listed. As stated above, there are many different RSO sizes from the many different suppliers, you really are flirting with danger trying to make your windows that exact. You may also find that adding in all the fractions to your dimension lines and labels may start to clutter up your plan too. -
Right way to do ceiling strapping with autoframe?
ValleyGuy replied to GeneDavis's topic in General Q & A
I came east from the west and thought that it was really different at first. There definitely are some advantages though. Having a completely open space with nothing but exterior walls and rafters to apply 20' wide poly is a lot faster than VB individual rooms or dealing with tie in wall plates from perpendicular walls. If the poly is tacked to the rafters only where the 1x4 will sandwich it to the rafter, there won't be any staple holes from the weight of the attic insulation. The ceiling doesn't receive any errant DW screw holes nor does it get any electrical wire or fixture box holes. Only stink pipe stack and sometimes HVAC penetrations, so it makes for a pretty tight ceiling. Push the stack through the roof and drop any necessary HVAC leads (plus the stack) below the ceiling level while the roof is being shingled. As the strapping supports the weight of the R50 in the ceiling, a double studded or ICF wall configuration means that you can have an insulated and VB house shell with the heat turned on before any back framing is done! Way nicer environment in the colder months. Any "extra material and time cost" applying strapping is more than recouped. I think it makes a much better built house having the heat on so early with the winter time builds. -
Right way to do ceiling strapping with autoframe?
ValleyGuy replied to GeneDavis's topic in General Q & A
Hey Gene, I went through this with Support a couple of years back. Strapping the rafters with 1x4 @ 16" o.c. is the industry standard here. At that time, and I believe it to still be the case, CA isn't able to auto frame 1x4 that is in the ceiling layers. I made and saved the two different 1x4 framing materials in my library and manually frame when needed. As the framing is actually in the ceiling layers, this was the only work around that I have come up with that keeps my top plate storey pole dimensions correct. Let me know if you find a solution, Shayne -
I agree, that Apple mouse is really only good for surfing the web or tasks involving little accuracy. I really enjoy using the MX Ergo S Plus roller-ball mouse from Logitech. For $140 CDN ( ... about $1.98 USD lol) it has 6 programable buttons and speed control for the curser. It is cordless, rechargeable, and has a roller wheel for zooming in and out. It's well worth it to invest in a good CAD mouse.
-
Good point, I'm pretty sure that my Mac Intel system will not support X17. So until I upgrade my computer, I'm stuck at X16. I also agree with other's request for more meat and potatoes. I'd be in favour of a version or two cleaning up and bettering some of the already established things in Chief, instead of starting new projects that will be added to the list of things needing some help and refinement. There are items in life that I purchase just because 'they work as they should' - not pretty looking, but robust and reliable. Get the job done efficiently type tools. Tech seems to always be expanding, but we are in a business type market that requires productivity needs over flashy extras. Somewhere CA tech will expand it's envelope far beyond what is really needed to get the job done and more people will say that they really don't need to upgrade. Maybe it is becoming more of a case of what do we want this program to do? Is CA spreading itself thin in some areas by trying to add in all the new tech advancements? I stopped buying new cell phones for similar reasons. I just want it to keep a contact list and make a reliable call (that stays on the phone and not suddenly jump to the truck) ... it is a phone after all. A lot of the flashy other things seem to become insignificant when I am trying to use the phone .....as a phone.
-
There seems to be two main paths to reporting SF information, basically because of the way the SF information is obtained. CA will split the walls between adjoining rooms, ex: the garage and house through wall will be divided evenly between the house SF and the garage SF (the same idea inside the house envelope, bath to bedroom,...). Some people are fine with this and some people are not. 1) If you are fine with it, you can use a macro in any one of the room's Object Information listings (code, comment, description, ...) and make a schedule to report that information. 2) If you are not fine with it, then the poly line method is another option. I use both methods for different schedules as well as a few macros to differentiate between New and Reno rooms, you can get as deep down the rabbit hole as you like / are able. Here is my method to accomplish both ways: 1) Room Reporting the Area: I programmed all of my room types to have a macro in the description. Room -> Object Info -> Description -> insert macro -> Global -> Room Info -> Standard Room Area. I then include the column 'Description' in my SF schedule (change the Description label to whatever you like). You can customize the schedule to include, or not, whatever room you like. It's dynamic and doesn't usually need any edits. NOTE: Making each new room retain the macro; there isn't an OIP (object information panel) in Room Defaults (little wrench) to add in the macro under description. To get around this I deleted all but one of the OOB room types. I made a room (in my template plan) as it does have an OIP, open up the room and insert the Standard Room Area macro in the description (I also added the Room Name macro in the comment and have the comment column in my schedule), and adjust all the data to fit the room; name, conditioned or not, flooring, schedule, ... While the room is still open, go back to General -> Room Type -> Define -> Copy. You can now change names and data as needed for every room you create. Save your template and you will retain all that information. 2) Poly Lines: I made a saved plan view and layer set for my p-lines in my template. They live there with all the programmed info, (macros, labels, colours, ....) and report to text box saved on a CAD sheet. The text box is my schedule and lists the info I want to report. The only real maintenance is to size the p-lines as you are doing now. I saved the CAD sheet on my layout, however, it needs a poke to properly activate - open and close a p-line (just one on the SPV) and open and close the text box on the CAD sheet. This will activate the p-line data and activate the calc's in the text box to show the proper numbers. I'm fairly new at using them too and can't stray too far into the deep end yet, so I'm sure there are lots of variations of how to accomplish little to no maintenance in streamlining the p-line task.
-
I used to import all of my freshly made wall types into my template, and just like Michael stated above... there becomes a lot of them. The interior walls are pretty consistent, it's the exterior walls that really seem to add up for me. The problem that occurred was I had a really long list to scroll through when in the wall specifications choosing a 'wall type'. I like to be able to control the plan view wall layers look and maintain control on all of the many different layer sets for all of the different walls created. I also like to have an accurate and dynamic wall schedule (exterior 6" wasn't quite cutting it). The same house may have many 'exterior' walls; walk-out basement walls, main floor walls, garage walls, garage to house through walls, second floor walls, dormer 'ghost' walls, attic to living space walls, attic to exterior walls. A lot of these you may want different wall component for, or different plan view looks, all for the same house. Some even take advantage of the new 'display layer' under the wall type for even finer control. Add this to the many different houses and the list gets exhausting. So I started putting them into my library under specific 'Wall Sets'. My library is always current and always on every plan... no need to chase after old plans to find the walls to import / copy. To get each of the specific library saved walls into the plan, just select the library saved wall and use it like the regular wall tool. I don't think that I really go into the 'wall type specification' list any more and it stays as a short list for each new template that I open. If I make a new wall (or set), I can immediately save them to the library and do not need to update my template plan but keep on working. I really like having specific house type walls grouped and in the library. Once that group is opened, all of that house's walls are on display just like a drop down list of wall tools. Another bonus is specific wall data is saved for each specific wall; whatever info you want to save only has to be created once. If I want a specific wall to be framed with a specific material so it stands out in a camera view, have horizontal girts of a specific size, specific macros attached, or I want the specific wall layer description in my dynamic wall schedule to be accurate, it's all there. Just remember that if you want to change a wall already drawn, don't just open up the existing wall and change the wall type as that will be the only data that you are changing. The description, layer, etc will stay the same. Draw over top with the new wall. I'm sure there are many ways and systems to accomplish this task, this one seems to work well for me.
-
As everyone above has said above, SPV's are really useful. Your team has already completed most of the heavy work by creating the different layer sets. SPV's just streamlines the process to maximize efficiency and organization with an extra hint of consistency, plus a measure of safety for errors and omissions. Here are just a few things to think about... Efficiency: - one click to change a lot of things; floor level, active view defaults, active dimensions, active layer set .... also, reference display. This is a big one for me, ref. disp. has it's own floor, layer set (colour, line weight, displayed items, etc), and stacking order, is saved in a SPV, otherwise one ref disp layer set will have to do all floor levels. - no time wasted sending any plan views to the layout. Each SPV is already saved on the layout and as soon as the layout is linked to the plan file, all plans views are updated instantly. Plus they remain active and current. - save time deleting errors because you forgot to change the active view and now you have the wrong sized text or the wrong note symbol... populating the wrong note schedule. Ever forgot to change the active dimensions or the layer set and now it asks if you want to display that layer because it isn't turned on... just one more pop up window to deal with before you draw the exact same dimension for the second time. Organized: - not all SPV's are for the layout. Overwhelming the customer shouldn't come from them watching the mouse do multiple clicks just to check a measurement or put a note onto the proper schedule, adjust the text size, or scroll down the long list of Layer sets. Professionalism is sometimes viewed by flow, rhythm and being organized. - If you have saved camera views to help save time and keep you organized, SPV's are very similar and just need to be set up and saved. This is my current SPV list, the "A" numbered ones are saved to the layout already and the ones w/o the "A" are for working / customer related reasons. Only the working / customer SPV's share the Active Defaults between floor levels and are arrowed up and down.
-
You got it, I have a Note Schedule on the CAD sheet that I send to the Layout as needed. The 'dumb' call outs are just CAD blocks.
-
2) consistent notes: This might help for plan Notes. I use a Note schedule on a CAD sheet saved in my template. I just add the note to the CAD sheet off to the side of the schedule (to be clipped out of the layout picture). I created 10" symbols and added them to my library. I use these library symbols to cover the symbol on the schedule (to keep both the schedule and plan looking consistent) as well as drop them into the plan as required. The schedule of notes will be the same every time this template is used or copied and the library symbols can be dropped into the adjusted / mirrored plan view as required. Save the CAD sheet in your Lay out template and you should be set. I have red hexagon and blue pentagon symbols for other note schedules.