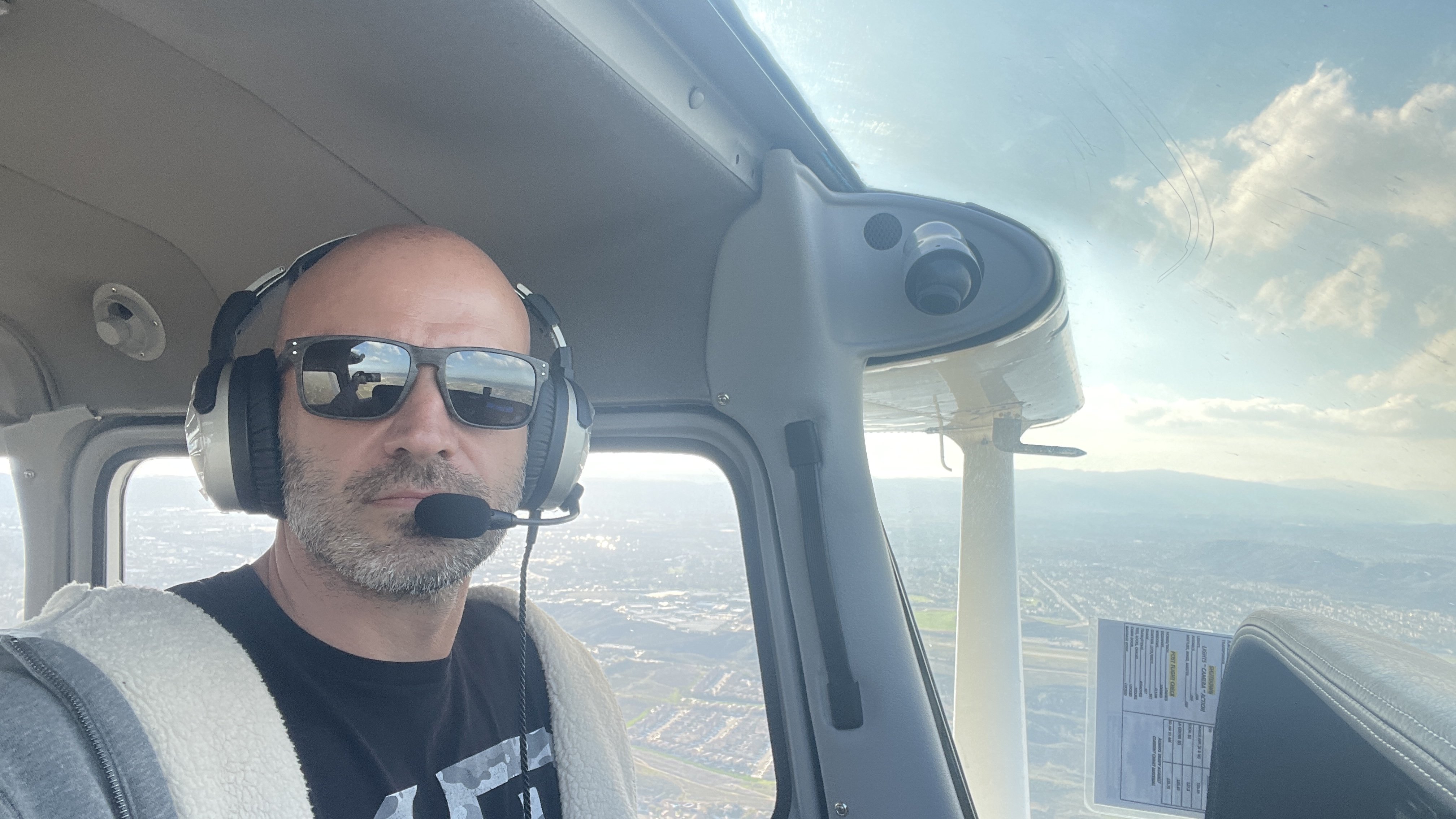
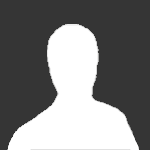
flightcrazed
-
Posts
37 -
Joined
-
Last visited
Content Type
Profiles
Forums
Gallery
Posts posted by flightcrazed
-
-
6 hours ago, JKEdmo said:
Be sure to give us an update on how this gets resolved. It's an interesting circumstance.
Jim
You got it!
-
On 3/15/2025 at 1:15 PM, JKEdmo said:
Very interesting post and it made me look at the code section again. It's complicated and I'd be interested if others agree with my take. I try to understand the purpose/spirit of the code instead of just the letter.
To me, the primary purpose of the WUI requirement is about preventing / reducing the ignition of exterior walls during wildfires. That's a bit different from the intent of fire rated wall assemblies which is to delay the passage of fire so as to allow for evacuation and first responder response:
So, to prevent wall ignition, the focus in on the wall covering, which needs to be non-combustible, "ignition-resistant" or fire-retardant treated wood. So, as long as the exterior wall covering complies, your non-rated wall complies.
But, say you decide to have a non-compliant (combustible) exterior wall covering. In that case, you have additional options, including but not limited to 1-hour rated wall assemblies. (This may be where the confusion comes from). Note these options are only triggered if the exterior wall covering is combustible.
Options include:
- You can also stick 5/8" Type X exterior-rated drywall behind the non-compliant combustible siding (common approach but not exactly a tested 1-hour assembly).
- You can build a (solid wood) log cabin or cross-laminated timber building.
- You could also have a tested 1-hour rated wall assembly with any kind of combustible siding (e.g. wood shingles). This is one option to comply with the WUI code but only needed in the case the exterior wall covering is non-compliant. In a sense this is overkill for WUI. But, your wall may already need to be 1-hour rated for other reasons such as proximity to property line. So you could just use this to satisfy the WUI requirement.
Jim
(Excerpts from 2022 California Residential Code)
Thanks for the reply Jim. This is my interpretation as well. On this project specifically, County Fire has requirements for maintaining 100' defensible space, the first 5' away from home of which are "most important". To me, that, combined with non-combustible/ignition resistant covering, should be sufficient for reducing the ignition likelihood of the wall during a wildfire (as you say, the intent) and meet the code requirements.
-
On 3/15/2025 at 8:39 AM, Gawdzira said:
In WUI areas I have not been asked for a one hour wall assembly unless the fire code demanded it for buildings inside of 10' separation. It seems like the exterior siding material having a WUI approval should be sufficient. I am very quick to shoot these questions to the AHJ.
3 things happen when I ask a question of the AHJ (building official)
1. I get the answer that covers my butt (and it almost always the correct answer)
2. I endear myself to the building official through being respectful of their authority and knowledge
3. I generally learn the thing and maybe some more via the answer
Thanks Alan. I have asked the County (Plan Checker) to answer the question but he is either on vacation or worried about responding :). I realize my mileage may vary depending on the inspector but feel like if my case is strong enough (plan check approved, code referenced, etc) then I should be good without having to tear down siding and adjust after the fact.
Appreciate your inputs as always.
-
3 minutes ago, richoffan said:
Seriously? Argue about fire resistance assembly in a woo zee? In California? Now? I got two building inspector certifications in 1994, just to learn to read the code better. The #1 thing stressed in both courses was know how to read the code.in its entirety Always check a definition as used in the code, especially if it is the determinate word. Better yet ask the AHJ
I mean, if we want to get technical...exterior wall covering includes Siding.
And your highlight refers to "finish" materials defined as:
So, there's that....
-
Hello,
Anyone with experience putting rigid Polyiso board over sheathing and covering with Metal siding? Curious if this is a best practice (using the polyiso as WRB) or if better to put a barrier between it and the wood sheathing and/or the metal.
Thanks!
Shawn
-
Hi all, hoping you can help me. I'm having a dispute with a contractor on whether a 1hr fire rated wall assembly or just a non-combustible covering is needed. The project is type VB, R3 use in a WUI area and not located within 125' of another structure or property line. I am interpreting 2022 CRC R337.7.3 to mean that only the non-combustible covering is needed (metal in this case). Am I missing anything?
-
1 hour ago, Gawdzira said:
I just spoke with a tech at Benjamin Obdyke. Both the Vapordry SA and the Cedar Breather products are class A rated. The documentation for Vapordry is forthcoming but it just passed the class A rating.
https://benjaminobdyke.com/product-systems/system-metal-roof/
awesome, thanks Alan. I'll check in with those guys. Do you have good experience with their products?
-
Thanks Michael, appreciate that. Honestly, i don't really find peace in either scenario: venting in a high fire area, or now unventing and having water problems.
Though pulling the UDL50 and giving a little breather to the top doesn't sound too bad at this point.
Underneath the roof deck, i'm a bit undecided on insulating at roof plane or ceiling plane now. Original insulation plan was 6" polyiso on top (none underneath) to keep the unvented design but since that has changed to 2" on top, I am thinking R30+ fiberglass batts in either roof or ceiling plane. The struct OSB does have a perforated reflective barrier (ceiling side). I think if i put in ceiling plane I'd have to ventilate.
-
Thanks for the reply @Alaskan_Son. Sorry, I didn't share full context, but there is a 2" layer of polyiso above the structural OSB followed by another 7/16 osb as a covering attachment layer. It is this attachment layer that has the UDL50 on top. The design principles for the unvented roof is how i arrived here...but seems like perhaps a metal roof shouldn't be installed above an unvented assembly (all of the "recommended" underlayments are low perm in nature, i.e. Titanium FR, Polystick XFR) if i'm understanding you right?
-
Awesome, let me know what you find. i'm still digging around as well and will let you know what i come up with
-
looks like the densdeck version might work...at least it's been tested by some metal vendors. i was hoping to find something a little simpler to install like 30# felt or similar
-
Hi all, working on a project that was originally designed to be an unvented attic with asphalt shingles. Plan is to change to metal, however the underlayment (Titanium UDL50) has already been laid and is only Class A under asphalt. I've found that Versashield can bring metal to Class A but not intended for unvented assembly.
Anyone know of another product that could be laid on top of UDL50 to reach Class A for metal? I've found Atlas FR10 but all the documentation seem to support a commercial roofing system.
Much appreciated!
-
Hi all, working on a project that was originally designed to be an unvented attic with asphalt shingles. Plan is to change to metal, however the underlayment (Titanium UDL50) has already been laid and is only Class A under asphalt. I've found that Versashield can bring metal to Class A but not intended for unvented assembly.
Anyone know of another product that could be laid on top of UDL50 to reach Class A for metal? I've found Atlas FR10 but all the documentation seem to support a commercial roofing system.
Much appreciated!
-
42 minutes ago, Michael_Gia said:
You can do a pony wall where the bottom portion is your 4” high concrete stemwall and the top portion is your barn wall at whatever thickness. Just be careful of how you’re aligning the top portion over the bottom one. I’m assuming you’ll want the outside to outside alignment, since you wouldn’t want a concrete ledge going around the outside perimeter.
The future 4” slab can go in whenever you want as the floor structure. I don’t think you need a floor finish.
That’ll be provided by the cows, I guess…
I'm not sure what “existing road base” is? Is that just your terrain going through the barn?
Genuis! Thanks for the reply! Yep, "existing" meaning by the time I go to pour concrete it would be existing.
-
Hi all, I'm designing an RCA barn and wanting to design the floors/walls to allow for a future 4" concrete floor sitting on top of (what would be) existing road base. I'll have continuous footings. Would I want to design a 4" high stem wall as thick as the wall in Chief? Or factor it in with either the floor finish or structure features? Much appreciated!
-
3 hours ago, M-Reed said:
Remember, you can place a support beam / header within the wall above in order to maintain the code minimum head room requirement.
Thank you! I did end up talking to my engineer who basically said, "don't cut into the top plates".
-
2 hours ago, Renerabbitt said:
well, 6'8 is code minimum because its allowable...same height of clearance as a door which we all have to walkthrough.
Without knowing the implications of the structural change its possible you could put a flush beam, consult an engineer.copy that. yeah, my door is 8' so i'd like to be closer to that. i'll check with engineer...appreciate the help!
-
17 minutes ago, Renerabbitt said:
That's probably my sloppy drawing :). Here's another view. Highlighted area is what i'm tryna figure out. Can i put header above plates (so i don't reduce the headroom from 7'3")? And is 7'3" even reasonable for living quarters upstairs (the only living quarters in this building)?
-
1 hour ago, Renerabbitt said:
Thanks @Renerabbitt for the help here. Sorry it's the white section with 7'6" measurement depicted here i'm struggling with. The 7'6 is top of the plate, 7'3 would be bottom (of top). Do i need a header under that as well? I'm nervous having such little head room as it is for moving furniture up the stairs.
Much appreciated!
-
Hi everyone, I'm designing a modern farmhouse style RCA barn with living quarters on 2nd floor and struggling with the stairs. My design calls for L shaped stairs beginning in the right "lean to" going thru the main center section wall as shown below.
I'm wanting to maximize headroom while allowing for proper structural needs (i'm not sure how high we can go into that wall). Obviously need to stay below the top of shed roof but question is how far below.
For reference, the 7'3" measurement on "Perspective Framing" drawing is from top of landing to bottom of double top plate. The 7'6" on cross section is to top of same plate. Nice to have: keep riser above 7" (close to 7 1/4")
Much appreciated team! Let me know if you need any more drawings/details.
-
52 minutes ago, Gawdzira said:
less likely to poison the workers. I can smell that spray foam for days and I always suspect if you can smell it, it is not your friend.
So true!
I do like the Zip sheathing. I did however find this on their website:
Despite their position, not sure why it would be any different than rigid foam. I am curious though, let me know what you find out from your engineer! I'll do some more digging as well.
-
I actually used this table in the CBC to come up with the R-5 (hoping to minimize costs
). According to this table, it seems "they'd" be ok even without spray foam if i went with a tile roof (Zone 3B) but I'm not a big fan of them. Also not sure that's a best practice. The foam I'm using here is R6.8 per inch which is more likely what the result would be (vs R5). But sounds like I should step it up to 1.5"-2" to get to the 25% recommendation?
I think i did find the drawings I shared previously from Building Science...was just looking for a reference to compare against my drawings.
-
On 4/11/2024 at 10:31 PM, Gawdzira said:
All of the unvented assemblies I have done so far have been Flash and Batt. I am in climate zone 3 so about 2.5" of spray foam (approx. r-19) and then batt to make up the difference to get to r-30. The spray foam goes in before the sprinkler piping to avoid a hot spray foam to piping issue.
For my next project I am looking towards something like you show #2. #4 looks expensive for construction and still gets you the fire issue for embers entering the assembly. With #2, either fill that soffit with spray foam or vent it. That is an area where you will have issues if it is left as shown.
Appreciate your help here @Gawdzira! How do these look? This would be in Climate Zone 3B
-
Fire rated wall vs non-combustible covering
in Building Codes and Compliance
Posted
@JKEdmomy County confirmed just the wall covering needs to be non-combustible/ignition resistant in my case. Thanks again for chiming in.