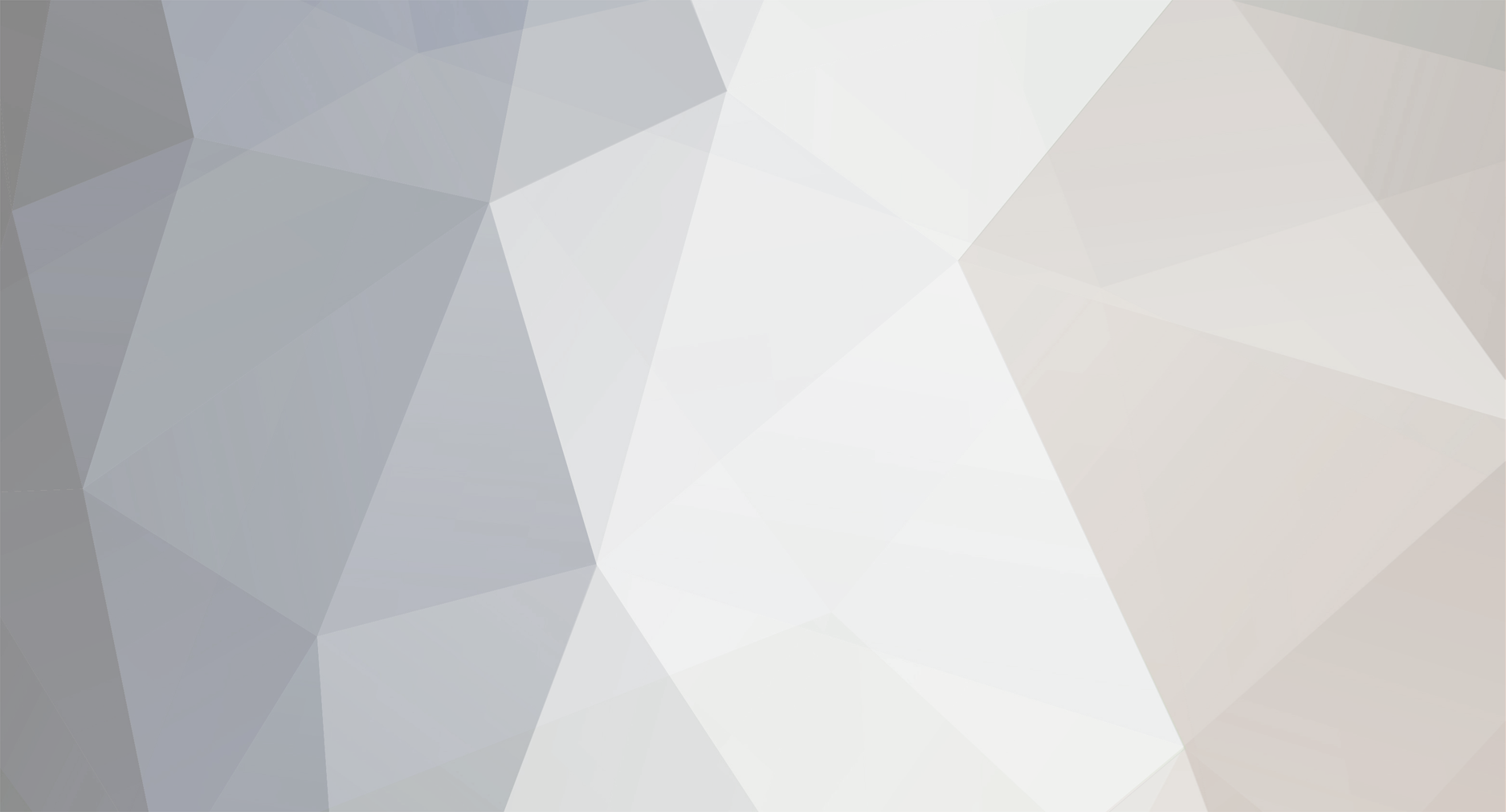
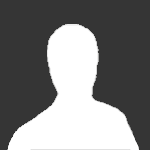
Jay_on_Cape
-
Posts
202 -
Joined
-
Last visited
Content Type
Profiles
Forums
Gallery
Posts posted by Jay_on_Cape
-
-
I always have anything automatic turned off. The 2nd step is everything I touch I make sure I fix on every level before moving on. If the great room was extended 4' I make sure I change the foundation then the roof, framing, cross section etc. before moving on to the next item. It's kept me out of too much trouble.....
-
Not that I'm aware of......... What is it you're trying to do where you don't want openings?
-
On the old forum there was a great link to a history of the releases. I can't find it.........I know I was using version 8 in 2002 so either it came out in 2002 or late 2001.
-
What kind of siding do you have? If it's vinyl you may want to up the wall sheathing thickness. It's a garage so you probably won't mind a few ripples if it's your own.
Check your roof sheathing. The stuff we use around here can't span 24" with just 1/2". We use 5/8" (or 19/32") with plywood clips.
You probably don't need flitch plates for your header if it's just an 8' span with 12' of tributary load unless you have a high snow load there or a floor above?
-
Anyone have some good plans I can copy? I might be able to sell them to a client and not have to do an work!!!
HaHaHa
GOOD plans? No, I have no good plans. Plenty of plans though...
-
So it seems like it's doable just takes a bit more patience and planning than regular. How did you display the building options and separate elevations (A, B, C, etc.) on the plans? Did you draw out each option in the plan and have a separate plan file for each completed option? Or did you have a separate option or elevation page that just showed the affected area you would go to then copy and paste it into the architecture?
I don't display options. I do know what you mean some national builders do that i.e..optional great room, optional 3 car garage, optional bonus room etc..
If sales sells a model "B" with elevation 4 I know I already have the model "B" and hopefully I have an elevation 4. I then open it up, make a copy to the specific lot and reverse it if needed. Then I go through the sales exhibit and change everything to that customer / lot. If you just look at one of my plans you couldn't tell there are numerous options or elevations.
My biggest problem when I started working for this builder was copying similar plans from houses we already sold. Inevitably there was a holdover option from the original plan that wasn't sold to the new customer thereby creating a problem. After a few burns I only copy templates with our standard specs already incorporated so when I get the sales exhibit I add their options and take out their credits.
With CA fairly stable now this is possible. Back in say versions 4-9 if you had templates built up and they came out with a new version and you upgraded you couldn't bring forward a plan without it going crazy. Especially if you reversed it. Now though, I haven't had a problem although I will still redraw all templates every 3-4 versions.
-
Version 4 didn't have any trim, for corner boards you buried a soffit in the wall with the control key. If I remember right it didn't even have any assignable layers. 97 was a big jump.
-
I've always had the take that people who are afraid to post the plan are, how we say.......not all that proud of it?
-
1
-
-
I would have contacted the Architect and asked him if he intended that the ceiling in that room be sloped? I would have done that immediately but I would not have told him I had discovered a mistake that he hadn't. This is a diplomatic way of pointing it out without saying it was a mistake. That would have given him the opportunity to deal with it without losing face.
Joe, I agree! That is why I said "diplomatically". Way back when I was a young and ambitious superintendent I pointed out an obvious mistake to a licensed architect on the project I was building. Even though it wasn't to show him up he took it as a very personal insult and his job (after billable hours of course) was to make my life miserable. After that I always passed the buck for other people (project managers etc.) to be the bearer of bad news. I guess you just have to know when you're dealing with a person who has never made a mistake and act accordingly... Hopefully they'll appreciate your effort to help them fix something before it is built.
Before CA cut out for doors in the foundation I used (and still do - over the plan generated cutout) a hatch pattern for the apron drop. Once I moved the garage door from front loading to side loading and forgot to move the hatch pattern. The lumber salesman let me know and I was incredibly grateful I was able to catch the foundation guy before it was poured.
-
I have used CA for my 7:30-4:30 job for the past 4 years. The builder I work for is a small (40-50 homes a year) production builder. We sell mostly (95%) off our rack models, mainly about 6 plans with various options. I have templates for each model I grab and make a copy of for the next house. Each of the plans has around 4-8 elevations so it takes awhile to create these templates. The template is a starting point with the correct elevation.
If I haven't drawn a specific model with a left hand orientation I open up the right hand orientation and save a copy and reverse everything, save it then copy it to change to the new specific lot plan. I don't have time to work on all of the plan templates so I do it on a as needed basis.
It's a good starting point. Then if there isn't too many lot / customer specific changes I can grab a template and have a complete house plan in 1/2 day or so.
On the side I still have my custom business where I provide custom plans for homes usually in the 3,000-5,000 sq. ft. range and CA works great for that as well
-
Before the fact? Diplomatically mention it to the builder. After the fact? Don't even think about it.....
-
I 2nd Kbird1 in that you should exhaust all local or in state designers / architects. If you're in New England and you hire someone over the internet in Arizona I promise you they will have a lot of things wrong on the plans. Way different construction techniques, different codes and even different methods of construction in the items that do overlap.
-
When I started with CA 18 years ago not only did I not have any cad experience I had 0 computer experience. I had to learn how to turn on a computer, open and save files etc. and of course install programs... I started by reading the book cover to cover. Back then it was a mere 500-600 pages. Read it like a novel knowing you won't retain anything close to all of the information. Then sit down with the program and practice. You'll then look up how to do certain things or watch video's to figure it out. By reading the manual you will at least remember that something is possible and you can refer back to the manual to refresh yourself how to do it.
I learned by spending each evening after work for 3-4 hours with no pressure from a deadline. After about 6-8 houses I took a 3 day course that really sent me on my way. If you take a weekend seminar before you're ready you will just slow others down and frustrate yourself.
Good luck!
-
...... I would never go to anything smaller than 3/16" scale, but the problem is everybody will pull out the 1/4" scale, leads to confusion.
If any carpenter told me they scaled my drawing instead of looking at the dimensions they would see a side of me they would be sure to not want to see again. You have to train these guys while they're young!!!
-
They have Diamond which is the same line. Masterbrand owns Diamond, Schrock, Kemper and Thomasville which are all the same line with different labels. The only difference is the name of the doors.
-
Not true, it has been discussed and reported ad naseum. It's just not fixed for some reason.
I must have tuned out previous concerns about this.
In baseball turns the introduction of the I-joist all those years ago was 87 feet to the bag and they're still not there..........
Why........I think I'm turning into one of the resident curmudgeons.....
-
Is anyone else having issues with labeling on Joist Direction Lines? I have 1 3/4" x 11 7/8" I joist and the label says 2x12.
This has always been like that since they introduced the ability to depict I-joists (maybe 2002-2003?). I'd like to say I'm surprised nobody on the board has commented on it in the past 12+ years. I noticed the 1st day I checked the new I-joist feature as about 99% of my jobs are I-joists.
-
Daydream,
I don't know what information you're looking for it could go in one of two directions. Are you looking for design instruction to be able to provide "design concepts" and not construction documents? If you provide design concepts for a draftsman / designer to complete construction documents from your designs than I would take the suggestions of others who have posted suggestions regarding books and college courses on styles and designs.
If you are looking to provide construction documents to homeowners and builders on a professional basis I would suggest you start by either working for another designer or a builder. Preferably a builder. They will teach you the basics to keep you out of trouble and provide you with more experience. It will take awhile to acquire this knowledge not just months. It sounds like you don't have the experience to know much if anything on how a house is actually built or structural loading paths. If you don't know at least the basics of framing you'll quickly exhaust all of your opportunities in your area when word gets out your designs are "unbuildable"......... When I say word gets out I mean that when you design a project(s) the CD's will end up at a lumberyard(usually 2-3) for estimating / EWP design. The salespeople, estimators and designers (EWP, roof truss, kitchen designer, window salesperson, etc.) will all critique your designs as far as code issues, specifications and structural possibility relating to their job. Their word then travels amongst themselves and their other builder customers. Never, ever underestimate the power of the lumberyard grapevine (I was an EWP designer for 4 years).
I'll give you a good analogy of "unbuildable". I was a private pilot awhile back but that's all I was. I am not an aeronautical designer. I'm sure I could design a "very cool airplane that looks absolutely beautiful"........ I am also certain it would be a very large lawn ornament incapable of flight.... Take pains and do it right. Don't run before you can walk so you don't become a lawn ornament designer.
-
I guess you are implying there should never be fractions in a plan ?
or are you saying if there are fractions you would never "hide" them ?
No, I'm saying I would never use "electronic whiteout". You fudge a dimension you have no idea what else is fudged in the dimension string or elsewhere. As an EWP designer I can't tell you how many drawings I had to design floor systems for that didn't close when I tried to just draw the exterior....Meaning someone (usually an Autocad designer) lied with one dimension and didn't fix it elsewhere.....When you get to the end of the drawing what do you do with all of those fractions or inches? Cut cabinets, doors, window trim etc. in the field?
On a related side rant I used to love the architects / designers who would still draft by hand (this was back in the 00's) and would dimension to both sides of the stud and figure 2 x 4's as 4"...........Oh that was a hoot! By the time you got to the other side of the house it would be off by 3-4 inches if you didn't move every one over a 1/4" thereby rendering each dimension inaccurate.......Ahhhh the life of an EWP designer......brings back memories....most of them bad..
-
I've got a question on X6 regarding dimensions and how to over-ride what's shown on the drawing?
For example, a dimension says "36'-01/8" and you want it changed to read "36'-0"". My old way is to use a text box, fill it with white color and a white border. Set it over the top of the errant dimension and then use Text layer and call out 36'-0". This is not a great way of over-riding the dimension. In AutoCAD, you have a way of doing this very easily. With Chief X6, there must be a way to accomplish this without all the extra effort?
I've been looking a the vids and cannot figure this one out? Is this even possible to over-ride?
As a home designer for the past 20+ years and a EWP designer for 4 years (where I had to work with hundreds of designers /architects plans)........I'd fire an employee who did what you're suggesting above....
-
I always show it on level 0. If you show it on level 1 then the model isn't correct. I assign all interior walls a different layer and turn them off for the foundation contractor.
-
Or set the ceiling height of that room to 48", build roofs then change ceiling to 9' and the roof will not move but the ceiling will.
-
See attached. White fill faded as a way to fade out the portion of the elevation that is not orthogonal to the camera.
Ahhhhhh, more of a shade tool than fill tool......henceforth my confusion.
-
Floor Plans - Hand Sketch Style
in General Q & A
Posted
I had Squiggle about 15 years ago! Is it still currently produced?