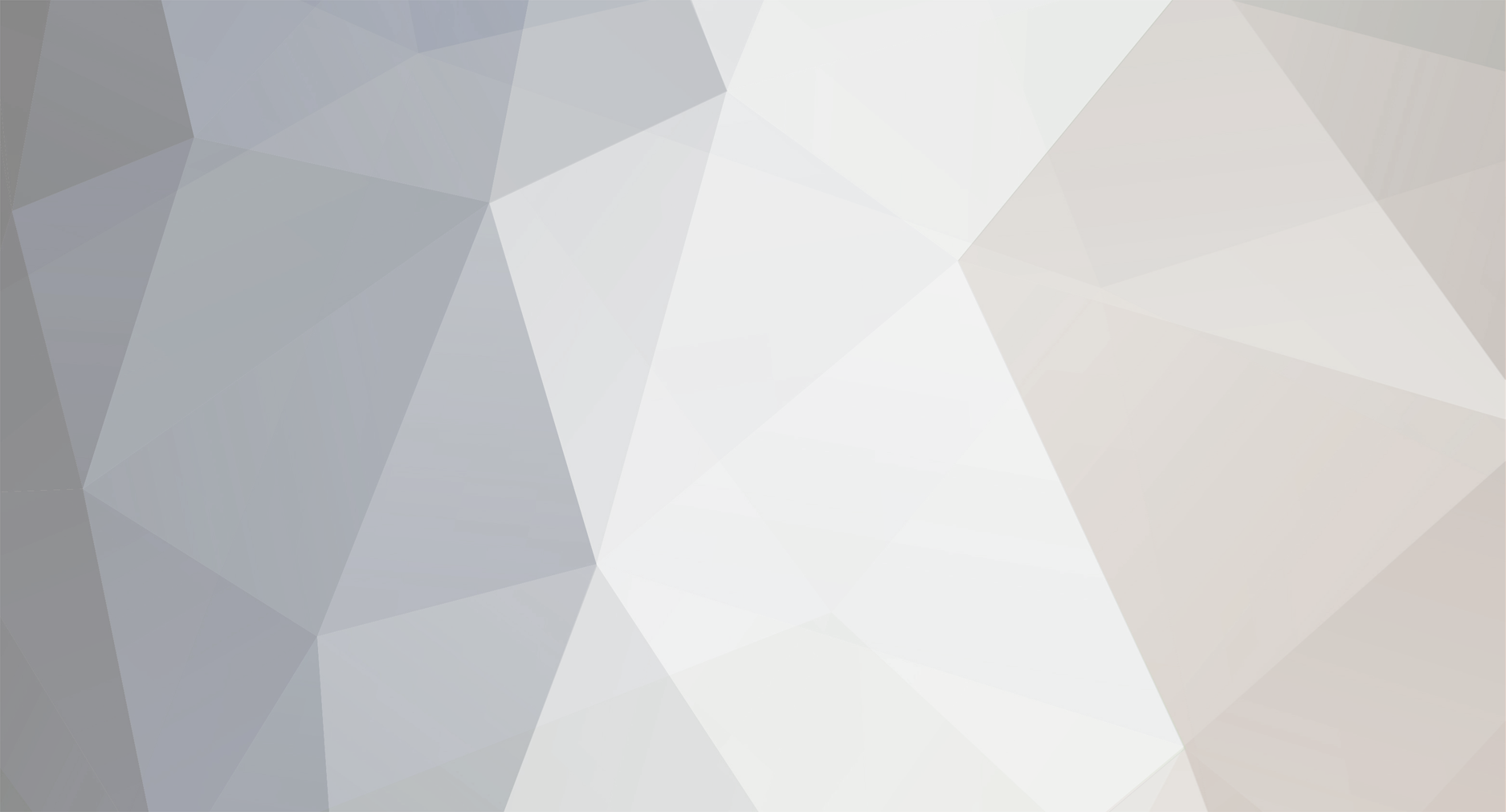
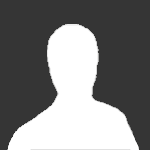
SkullMesaRanch
-
Posts
54 -
Joined
-
Last visited
Content Type
Profiles
Forums
Gallery
Posts posted by SkullMesaRanch
-
-
2 hours ago, rlackore said:
Your contours are problematic, specifically the 2437 and 2438 near the plan-NW corner of the residence. Make sure the new 2438 is connected at both ends to the existing 2438. Keep in mind that the engineer is providing a 2' deep swale, and he probably did it for a good reason, so I would strive to provide the same when you revise the grading. Also, your revised driveway is going to require some tall retaining walls along both edges, something the engineer's plan avoids by using a bunch of fill. So, pick your poison: an elevated drive, or a canyon drive.
Yes, these are the areas I don't understand. Where is the 2' deep swale shown? I just see 2440 around the house and barn. Is it the highlighted area shown in the screen shot below? Are these trenches?
The driveway doesn't need retaining walls, based on the neighbors driveways. I just need to shown the cut slope in the plan and don't know how. I have a soils engineer coming this week to test for stability. Hopefully resulting in more aggressive cut slopes than the county requires.
Thanks for the feedback, Robert, it helps.
-
Thanks to the help I received here and the CA sample building plan examples, my building plan was approved last week. It took a year to figure it all out but I was able to design my own house, generate plans, and get my conventional septic system approved without any "engineering." The county was extremely helpful anytime I had a question.
The one area I had to hire an engineer is the G&D plan. I've attached a screen shot of the plan I got from them after 5 months of waiting. I was never able to talk with the engineer directly, only the owner who is a surveyor. None of the input, like equalize cut/fill was taken into consideration. I ended up with a plan that required over 100 trucks of fill to be brought into this remote, difficult to access building site. The local excavator said it was ridiculous and all material should be generated on site. So I modified their plan, reducing the FF heights and cutting the driveway as I intended instead of creating a giant freeway ramp.
I'm not a drainage expert, although apparently I'll have to figure it out, but have to know how to route the flow. Can any drainage guys check this for me and provide feedback? I placed the FF height of the barn 1ft high than the house. I'm trying to avoid any flat ground for drainage purposes due to mud and horses. Creating a swale from the hillside through the 2 structures is not straight forward due to the difference in FF height. I tried to use the original plan as a guide but I moved the barn over to SE from the original plan
I know this isn't a CA question but you guys have come through for me so many times and I appreciate it.
Thanks, Beth
-
2 hours ago, solver said:
If that gives you the correct result, then why ask?
Because sometimes there's a box to check instead of doing it manually. This could help someone in the future that is searching for the answer to this question. Before I knew there was an automatic way to place the header at the top of wall, I was doing it manually.
-
I can't find a post or CA video that tells you what to do with interior non bearing openings. For 2x4 construction of an interior 30" door needs a 2x4 flat plate at the top of the opening. Is it correct to change the header (in CA) to a depth of 1 1/2" and the thickness to 3 1/2" with a single board? Is there a better way?
-
I gave up trying to keep my framing schedule format and just hit auto frame and all the headers were grouped properly. Problem solved.
-
I'm trying to finalize my construction plans and changed an interior door size to be the same as 5 other interior doors. Even though it's the same header size as the other doors CA gives it a different header label and places two line items in the schedule and parts list with identical dimensions.
I tried deleting the doors and replacing them.. and that worked. Except when re-framing some walls, now closet and window headers have the same problem. This has got to be something very simple but I just can't find it. How do I make all headers of the same size have the same "T" label?
-
On 9/21/2023 at 7:15 PM, richoffan said:
I essentially agree with Eric with an important variable. Split the trusses and connect on site. The major difference is the truss sections do not have to sit on bearing. The truss can be designed to be spliced on site either on the ground or during erection. The truss sections must be designed as one truss and the stresses on the splice addressed. Any truss designer should be able to accommodate this. The assembled truss only needs bearing at the "end" points - in your case 48' ± They can design the truss in multiple sections though this is far more complex but very doable. Have done many times over my career. Think about it - they're not using 48' sticks at the fabricator, they're splicing the chords some where. Anyway it's really not difficult, still easier than stick building with dimensional or TJI and you'll get what you want.
I pursued this path and finally gave up after two truss suppliers said no and the other two were not optimistic that they would do it. The engineers I talked to sounded young and had never split trusses without a bearing wall/beam at the splice. They all agreed to do it if I provided a bearing wall or beam. Since this exercise was like pulling teeth I decided to make a bearing wall and create an opening (beam) between the living area and kitchen. It only required moving a few walls 4.5" and now anyone can make the split trusses and my max truss length will be under 25'.
This was a good learning experience. The road has gotten a lot wider since I've spent the last 3 weeks cutting back palo verde trees with my chainsaw. Maybe now when I get an excavator out to do an estimate, he'll call me back.
-
-
15 hours ago, GeneDavis said:
Post the plan, give us your roof load specs for snow and live, and someone, me included, will show you how to truss it. Make sure we get the barn, too.
In the mean time, get your supplier's field guy to visit your site and scope out the delivery situation. I just did an i-joist roof frame in snow country with 110 psf ground snow load, but we have no saguaros here, only huge white pines. One lane curvy road going to. Driveway impossible turn.
I have someone coming today to work on my internet connection. Wasn't able to upload the plan this morning. Will try again later. I'm overwhelmed with the help I'm getting here. Thank you everyone, Beth
-
18 hours ago, solver said:
I don't understand. When I said wall, I assumed you would substitute beam for the opening between the living and kitchen, and that you would understand that the red line I marked does not need to be straight all the way across the house.
You need to sit with the truss manufacturer and explain the delivery issues, and let them design the trusses to fit -- they do that for a living. Your lumber company does not.
If you switch to a low slope (flat) roof, most will use trusses with the top cord sloped, and they will still need to be delivered.
I use Ballard Truss. They started local to me, but I believe they have locations around the state, and there are surely others.
Truss manufacturers often use extendable trailers for delivery instead of a standard semi trailer.
And consider asking for a plan review before you get too far. https://www.houzz.com/discussions/building-a-home is a good place.
If you make no other changes, could you flip the hall bath so you are not looking directly in from the living room?
I'll suggest this entire part of the plan could use a good rethink.
As always you're very helpful, Eric. I did fix that small bathroom, reversing everything so you don't see the toilet front the living area. Sorry for the old screenshot before it was fixed. As far as having a review on houzz, it's not like I can just provide a zip file for my CA file right? Is it just a floor plan review? This isn't a floor plan I dreamed up, it was taken from an existing house plan. You expressed your concern over the master bath. I didn't spend anytime with tile and finishes because I want to keep my file size small. The utility room is not showing storage space so it looks like wasted space. I'm more concerned about the structure, ease of build, and general functionality. There will be a lot of dirt tracked in and it needs to be easy to clean.
All other points are valid and very helpful. I talked with Alliance Truss and they're the ones that said they'd use a semi truck. Ballard is in Mesa but I will talk to them.
-
2 minutes ago, solver said:
The bearing wall doesn't extend on the left side of the structure.
As far as your other question, Eric... The lumber company said they would be transporting on a semi truck. Can the road handle this? I don't know how I can be sure of something like this and certainly don't want to take my chances.
There are 3 truss sizes (floor plan doesn't show the barn): 48', 42' and 32'. I've been given a lot of great options
Use I joist and build on site
Use half trusses
Build porches on site
or a combination of the above.
The only reason I picked trusses was to make the design and build easy. Using a flat roof with parapet wall is starting to sound a lot easier. I'm already using a ductless HVAC system (mini splits) so it's not like I need the space for anything.
Is it relatively simple to delete the roof and add the 2nd floor for a Santa Fe style home and barn?
-
2 hours ago, SHCanada2 said:
..beam and parrallel chord truss. cut the truss length by half
Thanks for the input. This would be beneficial if I wanted vaulted ceilings. The back and front porches could have a lesser slope and therefore cut down the length of the truss. The maximum length between bearing walls is 35'. I'll try post my plan but usually have problems.
-
54 minutes ago, Chopsaw said:
It might be worth having a discussion with the neighbors. They might be happy the road is going to see some improvements.
A 20 minute helicopter ride may be an option....
Or check with the truss supplier and they may be able to supply the engineering for I joists if they sell those as well.
Yes, most people would like the road improved especially when someone else is paying for it. Unfortunately there's a guy out there that does everything possible to keep people out. He had to wear an ankle monitor for a couple of years for harassing people.
The lumber supplier didn't give me any options but I also didn't ask. They definitely don't build trusses on site. I'll check with them and find out more about a roof I joist structure. I was going to use energy heal trusses so they sat on top of the porch beams. Can you have a boxed eave with an I joist structure?
-
I had my first construction document review with the county and was almost done with my plans. After meeting with my excavation contractor I realized it was going to be a huge undertaking to get the road in good enough shape to transport 48' trusses to the building site. Your allowed to perform maintenance on the road without a permit but need neighbors permission to do it. If someone complains...and the few people out there do a lot of complaining, the county has to get involved. I'm on my 3rd code violation report from the neighbors...none of which were valid.
So here I am asking for design advise. As far as I know you can't use roof rafters for this span. l really didn't want to build a territorial home with a flat roof but it looks like that might be my only option. I'd like to have a pitched front porch tiled overhang. Does anyone have an example of this? Any advise related to this subject would be highly appreciated.
-
12 minutes ago, JKEdmo said:
I'm a little surprised by this and you might want to double check his claim with your jurisdiction.
I took a quick look at your Cave Creek, AZ building department website. They say they're on the 2021 IRC and it seems it is still a requirement to slope garage slabs.
In my experience, a slope of 1/8" per foot is about as flat as you can go realistically...
Here's excerpt from 2021 IRC:
We use the 2018 IRC here in Maricopa county but it still has the requirement. I should have clarified my statement. The contractor said you can get a waiver for this requirement.
-
On 9/9/2023 at 2:13 PM, JKEdmo said:
I'm no concrete guy, but I'd assume so. To achieve the design it'd be a means and methods item and up to the contractor. You could also talk it through with a concrete subcontractor to see if there are any potential issues.
Thanks for the feedback, Jim. I just met with my excavation contractor and he mentioned that (at least in AZ) that slopes in garages are no longer required. I'll have to double check this with the county especially since they want to treat the barn like a garage.
-
On 8/15/2023 at 4:15 PM, JKEdmo said:
Charles,
Update -- ran it by my client and he elected to do no step down due to this very reason. Better accessibility.
Jim
This is what I plan to do for the garage and porches but the step is still required to make a slope in the foundation for water runoff. I watched a few youtube videos on constructing a foundation step down but none of them show the step only being tall enough to accommodate the sloped slab. I'm trying to figure out how this is constructed in the field and how many pours it takes. Can the house slab and porches/garage slabs be poured at the same time with the configuration I described above (no step, slope only)? Can the stem/curb wall be poured at the same time as the footings?
-
I spoke too soon. The method of changing the railing wall thickness to offset the porch post from the slab edge won't work. The truss is no longer on top of the post and is not supported. So I'm back to using the railing foundation (box checked) and setting the offset so that the post edge is 2" from the slab edge. This involves changing my foundation dimensions and complicates the foundation. Now the barn that was a 30X30 slab will now have an extra 2" concrete border around the porch (as well as the two house porches). Does that seem right or is there another way to have the porch post support the truss but still have a 2" border from post to slab edge?
-
56 minutes ago, robdyck said:
@SkullMesaRanchSimpson Strong-Tie Post Base; This is what I would use. In your case of a 6x6 post, 4.75" to the center line.
Thanks, that's what I'll use.
-
1
-
-
In order to offset the railing wall from the edge of the slab, I just changed the railing wall thickness. No need to have the foundation checked (turned on) for the railing wall. The thickness was adjusted so that the post center (5.5x5.5 post) will be 6" from the edge of the slab. This seems like a lot but if I use a 1/2" anchor than that's 12 diameters away from the edge. What do you use?
-
I was trying different options to see the effect of the variables. In all cases I forgot to add the continuous 1" rigid insulation (R=5) for stucco exterior. With R-13 it increased the results from 4% to 24%. I'm putting in good windows and doors so it comes down to the insulation. If I use R-21 in REScheck, I get 39% compliance. Joe, are you say there's no point of diminishing return?
-
I read through most of the REScheck posts but still didn't find the answers I was looking for.
How much margin do you design in for your compliance to REScheck? For example, If I use R-13 I get a compliance of 4.2% and if I use R-21 it's 22%. Of course, I should use the best insulation I can (it's my house), but just wondering what compliance margin is being used by others. This REScheck was done manually without CA export.
-
You guys are really helpful. I've been given a few options and even got an isometric from Alan. I'm confident I can now come up with a solution to this without changing the layout of the master bath. It's looking like a smaller window would help but a separate vent for the sink will solve the problem without any mods. Thank you, all!
-
16 hours ago, Bob-Roraback said:
Good relevant article
JLC Online Article PDF_ 0915b_JLC_CEV_L.pdf.pdf 8' 172.61 kB · 8 downloads
Thank you. Aren't sink traps 1.5"? This article implies that the sink vent line is 2" (due to the distance of 8' to trap.) Apparently they can be either.
My building plan was approved! ...grading plan has issues.
in General Q & A
Posted