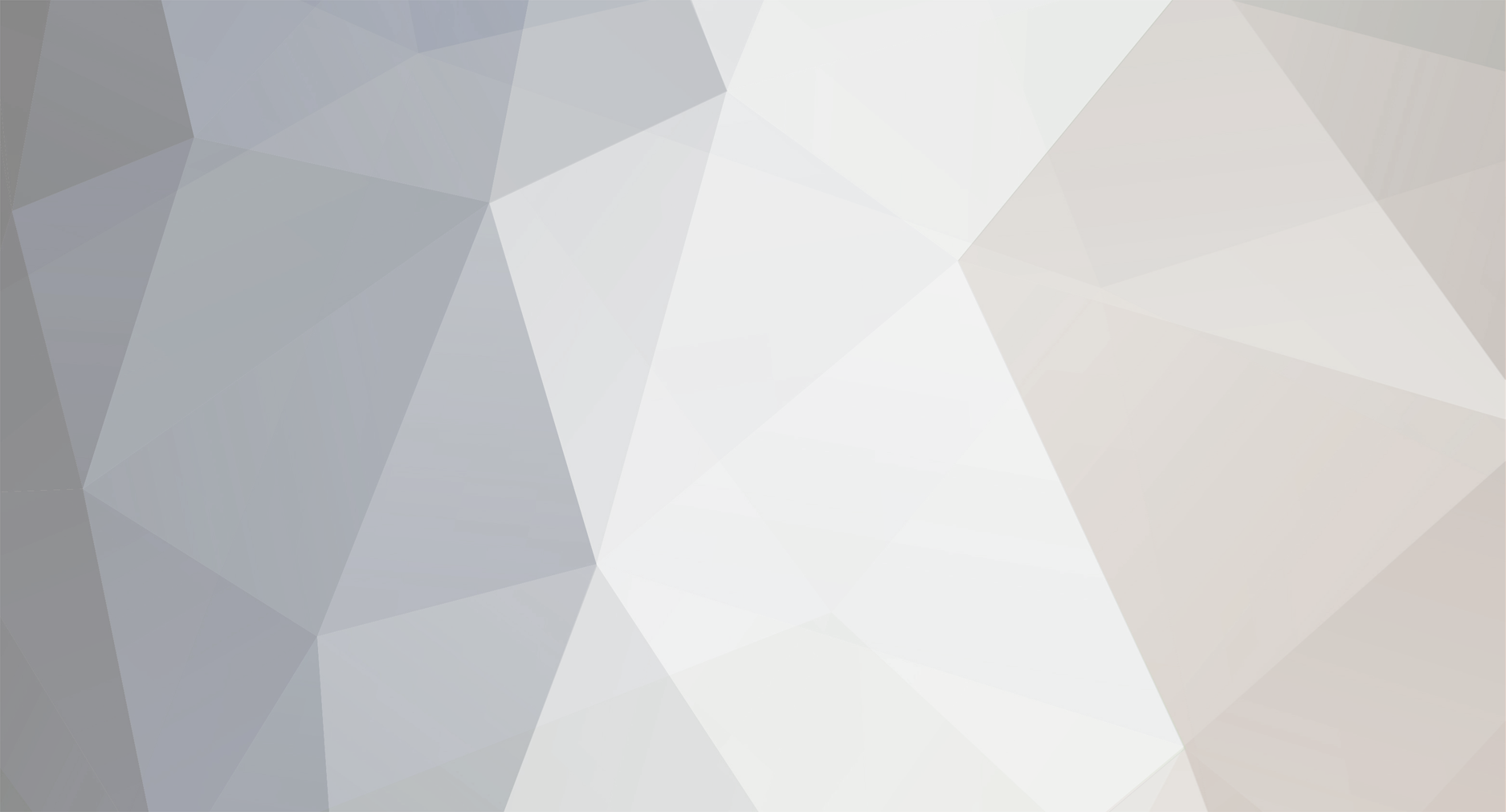
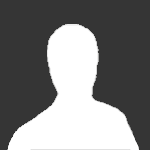
YoderW
Members-
Posts
19 -
Joined
-
Last visited
Reputation
0 NeutralAbout YoderW
- Birthday 08/13/1991
Profile Information
-
Gender
Male
Recent Profile Visitors
The recent visitors block is disabled and is not being shown to other users.
-
I probably am, I went to school for game design but focused on 3D modeling where they hammered into our heads that clean quad topology should be our priority. Admittedly I didn't do much in game engines, so I only recently learned that tris usually render faster. But Lumion support put such an importance on poly count when I was talking to them that I figured quads would be better. Thus why I started cutting out anything I could, even if it only saved me a few surfaces I figured every little bit helped. Since Lumion works a lot like a game engine, switching to tris may be our best bet. We don't usually do complex moldings or casings, as much as we would sometimes love to. I suspect our biggest problem is the custom symbols I've made for hardware and appliances, but I've optimized them as much as I know how to without losing quality. I'll look into it more when I have the chance, I know if I can find the time to learn how to make proper normal maps that can help a lot. My biggest hurdle is trying to make it as simple as possible for my co-workers since I'm the only one with an actual background in 3D. Thank you for the response and breaking it down like that, it helps a lot!
-
Thank you for your response! Yeah, I didn't think having two graphics cards would help us much unless we had a bridge. We've got dual-monitor setups, so each graphics card is going to a different monitor. If I understand correctly this should help split the workload if I have Chief on one monitor and Lumion on the other, but I can't tell much of a difference. I haven't been able to research it much, honestly. I suspected Lumion itself was probably the actual problem, I just haven't had a chance to test our models out in other programs yet. I just figured it would be easier to import our decor models directly into Lumion's library rather than bog Chief down and split all the faces into tris. And unfortunately, Lumion doesn't seem to phase the model at all. When I was talking to support, they implied that Lumion is essentially always loading the entire scene except when it's rendering a specific camera shot. We can use proxies for their nature models to increase editor performance, but that's it. I try to keep most of our textures at 2K or below, with 256x256 versions for Chief. I've been trying to push for us to switch to another rendering engine for a little over a year now, it's just been a while since we had time between projects to try and learn a new program well enough to introduce it to our workflow. Usually it slows down around the holidays, so hopefully we can soon. We've used Twinmotion in the past to show some of our homes in VR, but the co-worker that set all of that up moved to another department and we've been too busy to really sit down and learn the program ourselves. We were also looking at D5 Render at one point, but last time I looked they didn't have support for any of the file formats that Chief can export. I've tried using Blender as a middleman to convert all tris to quads which usually cuts the poly count in half, but it doesn't seem to help much with performance.
-
I've been toying with this on my own for a couple months, but I figured it was time to ask the Chief experts for advice. Sorry in advance for how wordy it may get! So for our workflow, Chief is just the starting point. We import a CAD file of a home's floorplan, build the walls, doors and cabinets, place appliances, make sure the exterior looks right, then export a Collada file and send it to Lumion to render. Lumion support pointed out that our house models are pretty high-poly, so I've been using trial-and-error to find ways to reduce the poly count of our models before exporting. Earlier this year, I tried importing a 3D symbol with mostly quad geometry and it would always come in broken. I spoke to someone from Chief's support team and got confirmation from them that Chief works entirely with triangulated geometry, both importing and exporting. They said the team might be changing that for X13, but during the first public demo another support team member confirmed that change hadn't happened. In case anyone doesn't know, triangulating a model effectively double the poly count which can have a severe impact on render times. Since Lumion works similar to a game engine with aspects of real-time rendering, this also severely impacts performance just trying to decorate and set up the house. Even with our 2080 Tis and 128 GB of RAM, it can get laggy pretty quickly. Occasionally I need to model and render some of our manufacturing plants, which is when these issues get much more apparent. So my question is, do you all have any tips for lowering the poly count? I've followed the Chief article about optimizing a plan to export to the 3D viewer, but even some of our simple homes still reach 1-2 million polygons (surfaces) by the time we're done. A lot of that is detailed custom 3D symbols for most of the hardware and doors, but that's mostly thanks to the requirement of tri geometry. Since our Chief use is entirely for appearance rather than function or structural accuracy, I've been trying to remove any unseen parts I can. We place furniture and decorate entirely in Lumion now to help with that. So far I have: Turned off nearly all the framing layers in the Camera View Set. I'm not sure which others are safe to turn off, but most of what's left are layers I know I need. Made sure none of the cabinets have shelves or actual drawers (though that sometimes increased the surface count?) Simplified the structural layers for the ceilings, roof planes, walls and floors. Typing it out that doesn't sound like much, but it's been a lot of small tweaking and figuring out fixes to new issues that pop up. For example, changing interior walls to one solid drywall layer means going into the door defaults Framing section and making the Rough Opening smaller, otherwise a gap shows above doors with a smaller casing. Do you all have any other ideas, or things you've tried to lower the surface count? I've hit a wall in my own testing, but I doubt I've thought of everything.
-
Is there any way to create a small gap or offset between the door and casing? Like a real door would have, to leave just a tiny bit of room for the hinges. Specifically for open interior doors. I've made a door hinge symbol I'd like to use, and I assume I'd have to make a different one for various swing angles, but I'm not seeing any obvious way to create that small gap. By default, Chief's doors just meet the casing at the corner completely, leaving no room. I could force the hinges in there, but they would clip through the door and casing and look less realistic. I'd also like to add a strike plate to the casing and latch to the door, but short of placing the symbols myself that doesn't seem very plausible right now. Maybe a suggestion for a future version of Chief.
-
Is there a way to make recessed lights cut only ceiling?
YoderW replied to YoderW's topic in General Q & A
For most it probably isn't worth it. But the copy/paste method you mentioned looks to be the way to do it. Our superiors and clients go nuts for photorealism wherever we can provide it, so hopefully this will add an extra "wow" factor. Purely for aesthetic purposes and photorealism, our Chief models are only used to export to Lumion for renders. Since we've started making 360 renders where clients can look wherever they want, I thought it would be a nice touch to have the recessed can lights actually recess into the ceiling. I haven't done much with actual ceiling planes, but I toyed around with that some and I seem to get the same results and issues I'm finding in my current method: It works, but I can't add the hole to the symbol's CAD block to automatically cut into the ceiling when I place the light. That was a good thought, though. Thank you all for your comments! I think the best solution currently is to place the light as floor mounted with an offset to match the ceiling height, add the hole in the ceiling, then select both and copy/paste as needed. It's a little clunky, but it'll get the job done. -
Is there a way to make recessed lights cut only ceiling?
YoderW replied to YoderW's topic in General Q & A
Here is a screenshot as an example. It's hard to get an image that reads well, but the light goes up into the ceiling a bit. This is with that last method I mentioned, so it's possible, but the hole in ceiling doesn't seem to work as part of a CAD block so I'm not sure how practical it will be to use. My hope was to set that CAD block as the symbol's default so it would create the hole anytime I placed the symbol and we wouldn't need to manually place one for every light in every home. -
Is there a way to make recessed lights cut only ceiling?
YoderW replied to YoderW's topic in General Q & A
It actually goes up into the ceiling by about an inch, so when I set it to be ceiling and flush mounted the ceiling finish covers the LED part of the light. The default symbols in Chief have the same issue, so they're not truly "recessed" which is most of what my company uses in their homes. It's not a major issue, but it would be a nice touch to have for realism now that we're creating 360 panorama renders of our models so I figured I would try to figure it out in my down time. -
Hello! I've made a custom symbol for recessed can lights, and I'm wondering if there's a way to cut a hole in the ceiling for it without cutting through the roof? We have started making 360 panorama renders for some of our home models at work, so I'd like to get the models as realistic as possible now that clients could look up into the lights. I've seen and done the method to create a CAD line and convert it to Hole in Roof/Custom Ceiling, but that creates a hole in both the ceiling and the roof, which doesn't look great for our exterior shots. We can make a separate model for those interiors if need be, but I'd like to just make one for everything if possible. I've also tried to just convert a CAD circle to a Hole in Ceiling Platform, but that moves the can light symbol up above the ceiling with the hole. Is my only option to use the ceiling platform hole and change the symbol to go off the floor's elevation rather than be ceiling mounted? Edit: New additional question, using the last method I mentioned with the hole in ceiling and the can light as floor mounted. Is there a way to add the Hole in Ceiling to a CAD block so it automatically creates that hole anytime I place the symbol? I'm trying the same method I've used for sinks to cut a hole in a countertop, but it doesn't seem to be working.
-
Controlling material names during a Collada export
YoderW replied to YoderW's topic in General Q & A
That's okay. That's what I thought, but I figured it was worth a shot to ask. Thank you! -
Hey all, Is there a way to control what Chief names each material as it's importing a model as a collada (.dae) file? At my company, we use Chief to build the base model and then export as a collada file to import into Lumion to render. Lumion's latest version has the ability to automatically replace materials with "glass" or "water" in the name with those kinds of materials when importing, but for some reason Chief will randomly assign names to materials during the collada export process like "mat127-material," regardless of what they are named in the material settings. Other export processes will keep the material names, but those have their own problems in Lumion. The 3DS format, for example, is the best alternative, but it changes the scale of the model. I can't seem to find anywhere in the preferences to mess with export settings, though. It's nothing that totally breaks our workflow, as it only takes a couple seconds to replace the material, but it would be a nice little quality-of-life feature we could take advantage of if we could get Chief to cooperate.
-
Hello! I'm working on a huge plan right now, and it's starting to run really sluggishly so I decided to take some time out to troubleshoot and clean up the file a bit. I've done a few suggested things (purge unused materials and CAD symbols, for example), and moved on to my layers. When I started the file, I imported all individual layers of the CAD file so I could work on the plan bit by bit, but it also resulted in a lot of unnecessary data being added to the scene. I'm trying to go through and delete all the layers I don't need or have finished with, but most of them won't let me. Some will claim there's still something on them despite nothing showing up when I hit Control+A, and others will switch to "Used in defaults," after I deleted everything on them. But I don't know what that means, and I can't figure out where in the defaults they're being used so I can turn it off. The layers that claim they aren't empty when they should be are bugging me, too. Control+A, zooming out and dragging a box over the scene never select anything for me to delete, but they still say "in use." I may be able to provide a back-up if necessary, though I'm not sure my company will allow it and, again, it's a very large plan. Can anyone help?
-
Custom dishwasher symbols not inserting into cabinets
YoderW replied to YoderW's topic in General Q & A
Okay, I think I got it now. Thank you all so much! -
Custom dishwasher symbols not inserting into cabinets
YoderW replied to YoderW's topic in General Q & A
Wow, thank you both! What did you do differently? The only thing I see that's changed is the size of the symbol in the object settings, but that should be stretching to fit anyway and doesn't fix it for my original symbol. -
Custom dishwasher symbols not inserting into cabinets
YoderW replied to YoderW's topic in General Q & A
I've tried messing with the origin both in CA and the original Blender file before exporting, but CA seems to ignore the Blender origins. I've attached the symbol as both a Chief library file (with the current best settings I can find applied) and the original dae. Low Cost DW2.calibz Low Cost DW2.dae -
Custom dishwasher symbols not inserting into cabinets
YoderW replied to YoderW's topic in General Q & A
I didn't think so initially since the dishwashers included in CA and the bonus catalogs didn't have them set up, but those seem to stretch on their own whereas mine won't. I've copied all the symbol and object settings I can find from one of the bonus dishwashers, but it still doesn't stretch in the X or Z dimensions. So I tried the stretch planes since that is what Evolution suggested I check.